Un catalyseur précis pour faire des produits chimiques durables
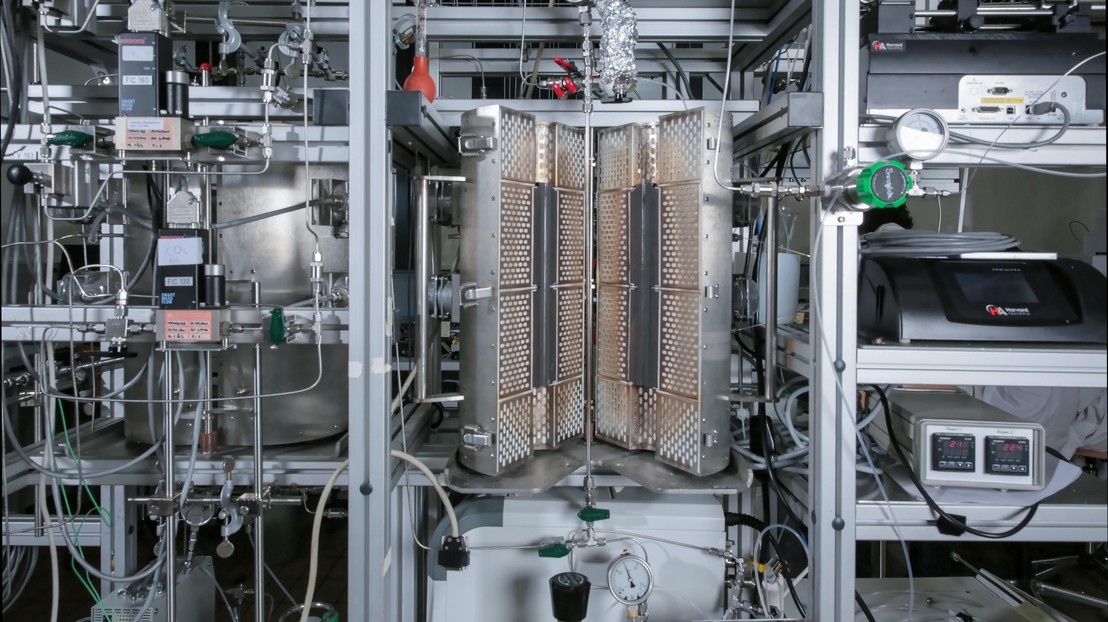
Le schéma de réaction utilisé pour transformer le dioxyde de carbone à l'aide de catalyseurs à couches précises.2024 EPFL / Alain Herzog CC-BY-SA 4.0
Des chimistes de l’EPFL construisent des clusters métalliques à l’échelle quasi atomique. Le procédé pourrait améliorer les catalyseurs, par exemple pour transformer le dioxyde de carbone en produit chimique à haute valeur ajoutée.
Des ingénieurs chimistes de l’EPFL ont développé une nouvelle méthode de production de catalyseur, motivés par la perspective de transformer des gaz à effet de serre, comme le dioxyde de carbone, en produit chimique à haute valeur ajoutée, comme le méthanol. Les catalyses représentent un outil crucial pour l’industrie chimique. On les emploie fréquemment pour la fabrication de produits pétrochimiques. Avec leur procédé, les scientifiques ont mis au point une manière de construire – à un degré de précision proche de l’atome – des clusters métalliques sur des supports solides, lesquels peuvent améliorer l’activité catalytique. Leurs résultats sont publiés dans Nature Catalysis.
«Il s’agit de fabriquer autant de produit que possible par heure et par quantité de catalyseur. Nous avons découvert que, lorsqu’un catalyseur est préparé à un degré de précision quasi atomique, on obtient un matériau plus actif», explique Jeremy Luterbacher, professeur au Laboratoire de procédés durables et catalytiques de l’EPFL. «Cette technique est particulièrement intéressante avec des réactions complexes, comme celle du dioxyde de carbone avec l’hydrogène gazeux pour obtenir du méthanol renouvelable.»
Quelques notions de catalyse
Bien qu’elles soient omniprésentes dans l’industrie, c’est généralement à travers le pot d’échappement de nos voitures que l’on prend conscience de l’existence des catalyseurs solides. Un convertisseur catalytique y convertit les fumées issues de la combustion du moteur et contribue à réduire la quantité de polluants relâchée dans l’air. Les moteurs des véhicules produisent notamment du monoxyde de carbone. Ce gaz toxique inodore et invisible, inhalé à haute concentration, peut entraîner des malaises, voire un décès. Dans la chambre, il y a un catalyseur, généralement composé de particules de platine ou de palladium sur un solide meilleur marché. Le métal facilite la réaction entre l’air et les polluants, comme le monoxyde de carbone, afin de relâcher dans l’air du dioxyde de carbone, moins toxique.
«Une réaction peut survenir sans catalyseur à haute température. Par exemple, brûler du monoxyde de carbone dans une flamme. Dans ce cas, la force de collision est suffisante entre le polluant et l’oxygène pour former du dioxyde de carbone, parce que la matière et assez chaude pour que l’impact soit suffisant», explique Jeremy Luterbacher. «Avec un catalyseur, le monoxyde de carbone et l’oxygène se lient à une surface métallique et réagissent, malgré le fait que la collision ait lieu à plus basse température. C’est un peu comme s’ils faisaient du patin à glace sur la surface du catalyseur, laquelle aide la transformation entre le polluant et le réactif.”
Les catalyseurs du futur devront transformer le dioxyde de carbone – un gaz à effet de serre qui représente la plus importante source de carbone renouvelable sur Terre – en gaz à haute valeur ajoutée, comme le méthanol. Ce processus se déroule à travers une réaction chimique appelée hydrogénation. Une réaction complexe, parce qu’elle peut produire d’autres choses que du méthanol. Il est difficile d’élaborer une catalyse à même de transformer assez rapidement le CO2 en méthanol sans autre sous-produit.
Un dépôt ultra-précis
Pour créer un catalyseur solide, on dépose une particule métallique sur un autre matériau qui présente une grande surface de contact, comme une poudre poreuse, afin de maximiser le contact avec le réactant.

2024 EPFL - CC-BY-SA 4.0
Jeremy Luterbacher et son équipe se sont demandé s’ils pouvaient maîtriser et accélérer les réactions en contrôlant précisément la composition du catalyseur. Par exemple, en sélectionnant exactement la bonne quantité de matériaux pour contrôler avec quelle force les réactants se lieraient au catalyseur. Dans uneprécédente recherche, ils avaient déjà découvert qu’il était possible de déposer sur des supports métalliques de petits amas de métal, à un degré de précision approchant l’atome. Cette méthode, baptisée liquid-phase atomic layer deposition (ALD), est idéale pour créer des sites précis de catalyse active, en vue de permettre une réaction.
De fait, en déposant ces petits amas de plusieurs métaux à une échelle quasi atomique, l’équipe de l’EPFL a pu hydrogéner du dioxyde de carbone à une vitesse plus de 10 fois supérieure à celle d’un catalyseur de même composition, mais élaborée sans leur méthode. Ils ont employé de l’oxyde de magnésium comme support – lequel se lie généralement de manière trop forte au dioxyde de carbone pour être réactif – qu’ils ont déposé sur des îlots de zirconium – un matériau qui se lie généralement de manière trop faible au dioxyde de carbone. Ensuite, ils ont ajouté du cuivre pour activer l’hydrogène. En combinant ces éléments dans de justes proportions, les scientifiques semblent avoir trouvé la formule idéale pour générer rapidement de grandes quantités de méthanol, et très peu d’autres sous-produits.
«L’oxyde de magnésium est largement reconnu comme un matériau stable pour capturer le CO2, mais sa forte affinité a limité son usage en tant que support de catalyse. Nous avons transformé cette limite en opportunité en l’associant au zirconium. Trouver l’équilibre optimal en combinant MgO et ZrO2, avec leurs propriétés différentes, n’a été possible que grâce à un outil puissant de déposition de couche atomique à phase liquide», explique Seongmin Jin, ancien postdoc au laboratoire et premier auteur de l’étude.
«Si nous comparons la quantité de matériau catalytique à sa teneur en cuivre, notre catalyseur se montre plus actif que ses homologues commerciaux. Notre activité par site actif est également supérieure. Mais il est important de noter que par rapport au poids total du catalyseur, notre activité reste inférieure à celle des équivalents commerciaux, parce qu’il nous faut encore trouver un moyen de générer beaucoup plus de clusters sur la surface. Nous avons toutefois montré que l’on peut atteindre une maîtrise élevée à l’échelle atomique – une maîtrise qui s’avère très importante. Elle ouvre la voie à de nouvelles possibilités et à des explorations en termes de combinaisons de métaux», conclut Jeremy Luterbacher.
https://www.nature.com/articles/s41929-024-01236-y