Solar Thermal Panels: Black is Back!
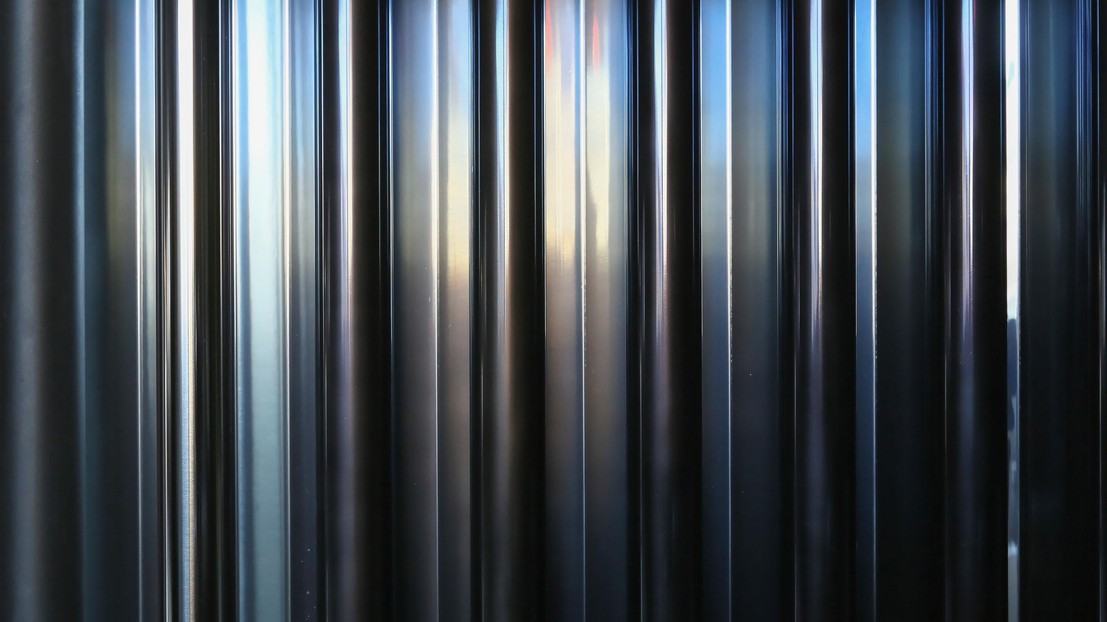
© 2014 EPFL
Solar thermal panels developed at EPFL are are dressed up in unique and patented new materials. Researchers created a stronger black coating that retains its original color and thereby its absorption properties much longer than traditional panels.
Like most elements of a building, the lifespan of a solar thermal panel is between 25 and 30 years. To slow the aging process and maintain their performance, a team of researchers from EPFL have, in rapid succession, improved the black coating used for thermal sensors and developed an original and patented method for depositing the coating.
The color black is at the key element of thermal panels because it can absorb up to 90% of the energy it receives. However, over time, the effects of light and heat deteriorate the black, and the panel becomes less efficient. Engineers have developed an innovative process that deposits thin layers of 3 different materials that are more resistant, more selective and less toxic than the chromium used thus far. As such this new material provides high durability in the open air at temperatures of 300° C to 400° C, thus avoiding the use of glass vacuum tubes, which are expensive.
A new black coating
Martin Joly, of the Laboratory of Solar Energy and Building Physics, researched a novel process for the conversion of solar thermal energy. He developed a nano crystalline coating which shows exceptional resistance to high temperatures. It abandons the black chromium that was used for panels currently on the market in favor of a multilayer composite of cobalt – for its corrosion resistance, manganese – for black, and copper – for its thermal conductivity.
“We wanted to develop selective layers that absorb light well and that are less toxic than chromium. That’s why we followed the trail of these materials.” Layers deposited by a chemical process boast an exceptional heat resistance that was never achieved with traditional chromium coatings. In fact, they can withstand temperatures of 360 degrees Celcius without deteriorating in contact with air.
For a flat sensor, the actual average temperature is about 80° C, and in summer the temperature can reach 200° C. Regularly exposed to air and moisture, the sensor must last for 25 years on a building, which is not so easy.
“The durability of our materials at temperatures exceeding 360° C could also be of interest to thermal power plants,” says Andreas Schüler, who heads the research team.
From nanoparticles to full-scale prototypes
In order to cast the 3 different elements in thin and homogeneous layers, the researchers did not hesitate to work in full scale: “When researching nanoparticles, you normally use samples. For us, we set the challenge to coat 2 meters long stainless steel tubes,” explains the researcher. To achieve this, the scientists had to build suitable machines for their project.
Materials are deposited by successive dipping, and each layer is heated by induction which evaporates the carbon and fixes the elements. “We started by buying simple resistors then tried induction and obtained results that far exceeded our expectations,” says the researcher.
This method has the advantage of being rapid, with impressive energy efficiency and an improved quality in the results. And the layers are perfectly deposited and homogeneous. What’s more, a patent has been filed on this new method. The work conducted by Martin Joly has resulted in two publications. One in Solar Energy, on the black chromium-free components and their optical properties, won the best paper award from 2012–2013.