Seed bioscience — A collaboration between design and technology
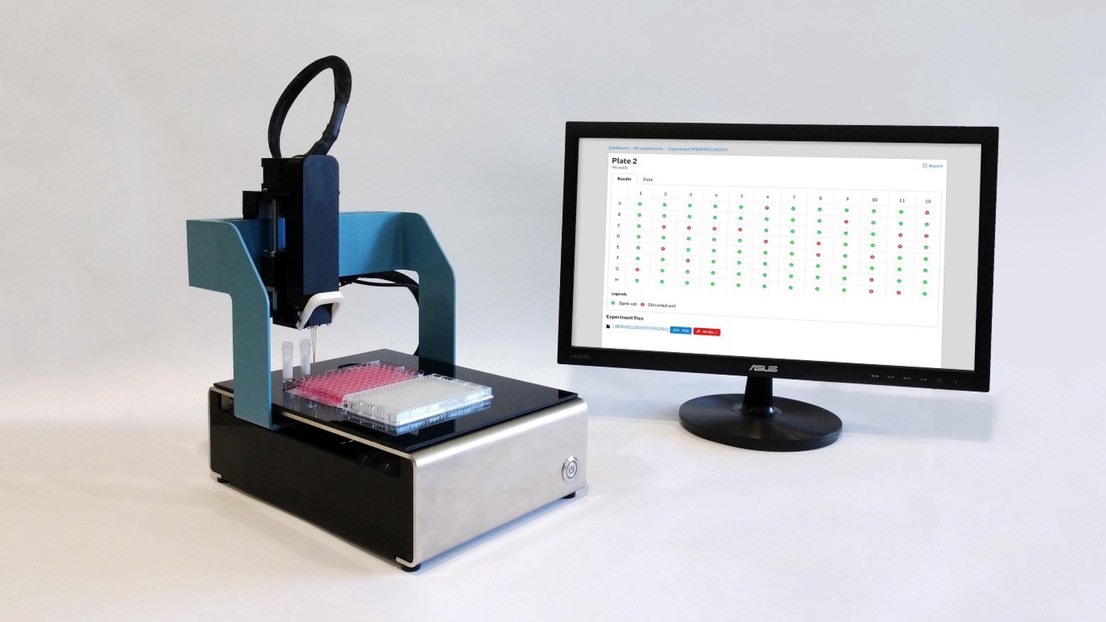
© Seed Biosciences
The SEED Biosciences project was a year-long collaboration between product design, graphic design, engineering and business made possible by the generous support of the enable program at EPFL and the Gebert Rüf Stiftung Designplus grant.
Background and technology
SEED Biosciences is a swiss start-up that has developed a novel technology for traceable single cell isolation. For the uninitiated, single cell isolation is a key enabling step in many biological processes like cancer diagnosis, stem cell therapies and personalized medicine.Present practices of isolating single cells are non-traceable and have long validation time. SEED Biosciences’ technology allows accurate traceability compliant with the most stringent regulatory standards and is up to three times faster than present methods. The core technology is embodied in the form of a simple pipette tip.

The Design Story
The collaboration with design started with the idea of embedding the technology in a hand-held pipette — A pipette being the natural extension of a biologist’s hands would have made using the technology more intuitive. However, responding to customer needs of large throughputs and accuracy, the team quickly pivoted to the design and development of an automated pipetting system. Their first product is called Dispencell. It is a robotic system that pipettes single cells into multi-well trays.
The design of a robotic system presented many challenges — How would it be made (hardware)? How would it be used (interaction and software)? And how would it be embedded in the existing landscape of the laboratory. Design, engineering and business worked closely together to address these.
The team envisioned that single cell isolation should be as simple and intuitive as using a mouse — point, click and single cell. With this in mind, while the engineers set to work figuring out how to make the robot work and putting together the first demonstrator, design dived deep to understand the context and needs of the users. After numerous visits to cell labs and shadowing technicians, the designers were able to understand not only the behaviours and anxieties of those working with cells, but also the constraints of working with biology. For example, sterility was scared to the scientists and lab technicians working with cells; experiment data and lab inventory were maintained in an Electronic lab notebook (ELN) and an extensive Laboratory Information Management system (LIMS/SLIMS); and that some of the consumables for the single cell isolation along with the cells themselves had to be stored in temperature-controlled environments.
This rich understanding of the landscape helped set important constraints and raised critical questions early on. Firstly, the size of the robot had to be limited to what fit into the sterile hood. The hoods have a glass barrier in front to blocks external airflow and hence contamination — what this barrier also limited is a person’s reach into the hood. The Dispencell robot had to be designed for this constrained access, using materials that would be easy to clean and non-porous, such as to not become a breeding ground for bacteria or fungi.
An additional constraint came from the business side. SEED Biosciences was an early stage start-up, just beginning to attract investors and had limited funds. It was imperative that it be possible to produce both the robot and consumables in small quantities — giving the company the agility to adapt and change their product without the risk associated with large investments.
The resulting robot was made in stainless steel — a standard sterile material found in laboratories, very easy to clean and maintain. Most of the internal components were off the shelf and supporting custom parts were cheaply 3d printed. The body was made by CNC sheet metal bending in collaboration with a local company and assembled inhouse for the initial 5 robots.

You remember that the technology was in the form of a pipetting tip. It turned out that the golden strip on the tip was quite fragile and scientists were reluctant to touch the tip with their gloved fingers for fear of contamination and damage. A tip cover had to be made to address this. Though the end result was quite simple, the process of getting there was anything but so. The cover like the tip itself was a single use disposable item. Besides protecting the fragile tip, the cover needed to be compatible with the pipetting head on which the tip was eventually mounted and be possible to produce in small quantities in a material that could be sterilized by the ethylene oxide process. Phew!
Eventually after much trial, failure and frustration, we figured that the ABS filament of the FDM (fuse deposition modelling) method of 3d printing was found to be a compatible material for the tip cover. A minimal design for the cover was developed such that it would use the least material possible and be produced in the least time. The tip covers were designed to be eventually injection molded, but were produced in ‘vase’ mode — a much faster method in FDM printing that extrudes a continuous spiral of filament instead of depositing the filament layer by layer.
In parallel to the hardware aspects, it was important to think about how scientists and lab technicians would use this robot — what would the controls be like? How would the results be communicated and available for downstream cell processing? How would the robot plug into the existing LIMS/SLIMS ?
Keeping in mind the steps needed to isolate single cells using SEED Biosciences’ technology and the understanding of how people work in a lab, a plethora of possible journey were mapped out. Would the robot have an operating computer attached to it in the hood, near the hood? Or could the robot behave like a common printer connected to the LAN — people sending print commands (in this case, dispense commands) and then hopping onto the robot, selecting their experiment and running it? One thing was clear — the robot was a common resource for a group of people. The interface and interactions had to address this need.
In the early days, the interface for running the robot were hard lines of code. With design coming in, it was imagined as an easy to use, touch screen interface connected to the local network of the laboratory (LIMS/SLIMS). A windows surface computer was used that saved a lot of space in the hood and provided mobility. Being connected to the local network meant that one could plan and design the experiment remotely while the machine was dispensing cells for another person.
A detailed user journey was established, the functions of the journey mapped to location (whether they needed to be done remotely or on the robot itself), and the possible error and pain points identified. This led to the Dispencell app having a 3-part architecture comprising of the following functional layers
1. Design — to plan and save an experiment
2. Dispense — to select an experiment and run the dispense cycle on the robot
3. Results — to view the results of an experiment.
In addition to the app, the error and anxiety points identified in the process lead to design adaptations on the hardware front for greater clarity, eliminating confusion and the possibility of errors.
Further collaboration with a graphic designer made it possible to have clear and consistent visual communication on the app and around the technology. A branding strategy and all the collaterals were developed including the website. A packaging system for all the disposables was designed and made for the first customers. The visual design work gave the hardware, interface and the company one unified personality.
The Design Impact
Design brought a lot of silent intangible attributes of great value. Firstly, by thinking about how the technology could be embedded into the current physical and digital landscape of the lab and making it easy to use, adoption barriers were lowered and this made the technology very attractive to early customers. Secondly, design working together with the internal business needs meant that the risks were kept low. And thirdly, design brought coherence to the system and a sharpness to the quality of communication of SEED Biosciences.
Today, DispenCell is hard at work in labs across the world. The technology is helping organizations such as Sanofi and Merck with their research into oncology and rare blood disorders.

The Team
CE0 and Co-founder — Georges Muller
CTO and co-founder — David Bonzon
Engineers — Luc Aeberli, Nicolas Uffer, David Forchelet
Business Development — Charlotte Broennimann.
Product & Experience design — Sumegha Mantri
Graphic Design — Ilina Catana
Photographs — Julien Deceroi
This project was supported by the service Design and Prototyping of the Startup Unit EPFL