Retreeva a startup that retrieves lost gold and cuts carbon emissions
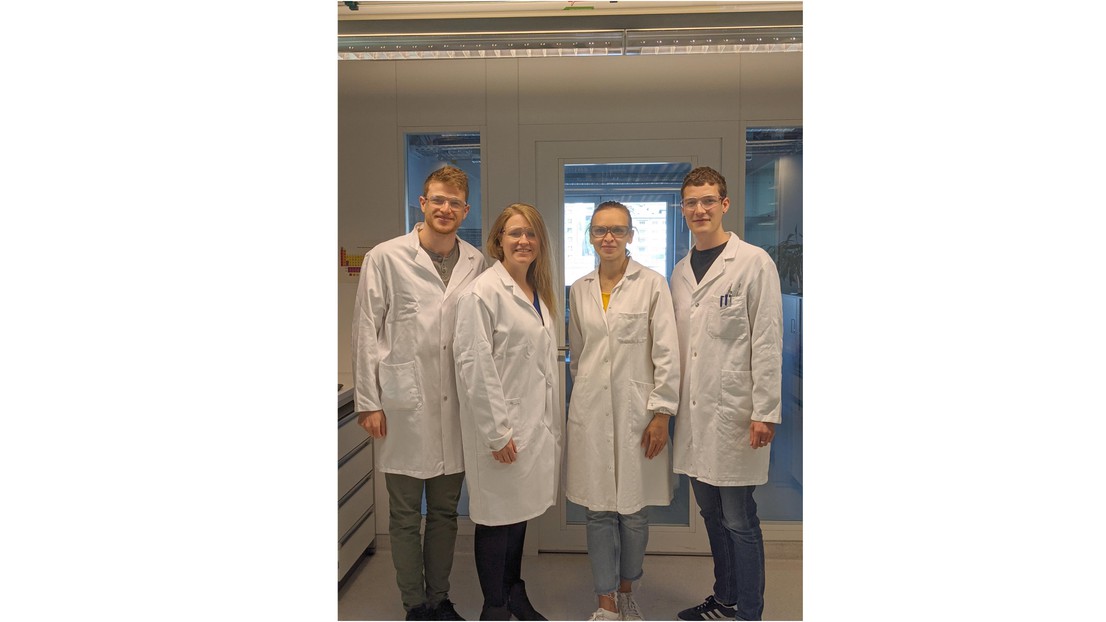
© Retreeva team 2021
Gold is big business. The metal is used across industry – in our cars, medicines, electronics and to fill our teeth. But all that gold comes at a cost. The mining industry is one the world’s largest sources of carbon emissions. It is estimated that mining accounts for around 10% of the world’s energy consumption.
Retreeva, an EPFL startup led by Dr. Olga Trukhina and Professor Wendy Queen from the Laboratory for Functional Inorganic Materials (LFIM), has developed an innovative solution for recovering the trace amounts of gold lost during production and returning it to the production cycle.
Throughout history, gold has been synonymous with prosperity and wealth. Most of the world’s gold supply comes through Switzerland at some point. In 2017, 2’400 tonnes of gold (70% of the world’s supply) were imported to Switzerland.
However, mining consumes 10 percent of the world’s energy and is one of the biggest contributors to global carbon emissions. Amazingly, during the manufacturing, at least 1% of the gold is lost – 58 tonnes a year. This doesn’t take into account all the gold lost to landfill as thrown away old mobile phones, laptops, and tablets. With gold costing around CHF53 a gram, these losses add up to big money very quickly.
The demand for gold is not going away – with a society increasingly reliant on electronics, our need for gold is likely to increase. However, gold is not an infinite resource – the amount of gold still available to be mined is estimated to be around 50’000 tonnes. With 2’500 – 3’000 tonnes of gold being mined a year, that means our gold supply will run out in about 20 years.
We spoke to Olga Trukhina to find out more about how Retreeva technology can find, recover, and recycle gold - saving 3.7 tonnes of carbon emissions each year.
What’s the purpose of Retreeva? What problem are you solving?
Gold production is a hugely intensive process. Large amounts of rock need to be mined and processed just to produce just one ounce of gold. Mining is one of the largest sources of carbon emissions globally, consuming 10% of the world’s energy, largely through the burning of fossil fuels.
Once the gold is extracted, it moves along the production chain to be processed and refined into gold ingots, or gold bullion bars. It then moves onto manufacturers of products like fine jewellery and electronics. As the gold is refined, processed, and transformed into products, up to 1% of it is lost in industrial waste streams – either in the form of discarded rock, dust, sludge or as part of water waste. In total, all this lost gold is equivalent to $3.5bn per year.
Our new sponge technology enables industries to retrieve trace amounts of gold from liquid waste streams more effectively, allowing them to potentially bring billions of dollars’ worth of gold back into production.
What motivated you to develop Retreeva?
As chemists, our main motivation is to enable a new approach to recycling valuable precious metals while helping to reduce the environmental footprint of the gold industry. If you think about it in numbers, it requires as much as one tonne of mined rock to obtain 1 to 10 grams of gold, depending on the type of a mine. Hence, with the recovery of 1 gram of lost gold, our technology can prevent up to four tonnes of CO2 emissions.
The mining industry also uses chemicals like cyanide as it processes gold. This produces toxic waste which causes further environmental damage. If we can reduce the dependence on virgin mines, we’ll quickly see a huge saving in energy use and a vast reduction in the carbon and chemical footprint of the industry.
How did the project start?
We were initially working on a solution for water decontamination – aiming to develop high performing materials that might allow people in the world’s poorest countries to access clean drinking water. As part of this project, we developed a novel adsorbent, a sponge, which effectively extracted toxic metals from water. We quickly realised that by changing the structure of the sponge, the same technology could be used to retrieve precious metals from liquid waste streams and plug them back into the production cycle.
How does the technology work?
We’ve created a new generation of adsorbents with a unique chemical structure; these are metal-organic frameworks infused with polymers. They are able to selectively extract targeted metals, like gold, from complex liquid mixtures. The two parts work together to retrieve the precious metals. Put simply, it is a water filter – filtering out precious metals which can then be recycled.
How does it differ to existing technology?
The surface area of our sponge is around 100 times higher than the solutions currently used in metal refining and processing industry. As a result, we outperform the existing processes both in terms of the volume of metals we can retrieve, and how effectively we can separate the metals from each other. Because our sponge is more efficient, less of the material is needed to do the job, so production and disposal of the sponge itself can also potentially offer a smaller environmental footprint.
Are there any other sectors where your technology can be applied in the future?
Our technology can be applied to any sector that loses precious metals in the production and waste cycle. We particularly want to address recovering precious metals from electronic waste. Many of us are guilty of throwing away old electronic devices – when we upgrade up phones, buy a new tablet, or replace obsolete technology.
This electronic waste is a growing environmental issue – in 2018, over 48.5 million tonnes of electronic waste was produced and ~80% was not recycled. This electronic waste is rich in precious metals like gold or silver. Every year, Americans throw away phones containing over $60 million worth of gold or silver!
We also think there’s potential in the recovery of precious metal from liquid waste and solid waste. Studies have found incinerated sewage sludge can have similar concentrations of precious metals to the metal ore found in virgin mines.
You’re currently based in EPFL’s Functional Inorganic Materials Laboratory. How will the Innogrant help you?
We will use the year to work iteratively with our future customers. Our technology has the potential to be a game changer. But it is key we nail down how our customers can use it. We’re going to work closely with key contacts in the gold industry to validate and evolve our technology.
What are you most excited about for the future?
We can’t wait to bring this incredible technology to the market – one which we hope will make a real impact. We want to make the precious metal industry more circular, less dependent on virgin mining, and less impactful on the world around us. We also know there are waste challenges which companies haven’t started to think about yet – so, we want to take the lead and develop technology-led solutions to solve these future threats to our planet.
Retreeva is based in EPFL’s Laboratory for Functional Inorganic Materials, which is directed by Professor Wendy Queen.
For more information on Innogrants and details on how to apply, visit the Startup Launchpad website.