Predicting hydraulic fracture propagation more accurately
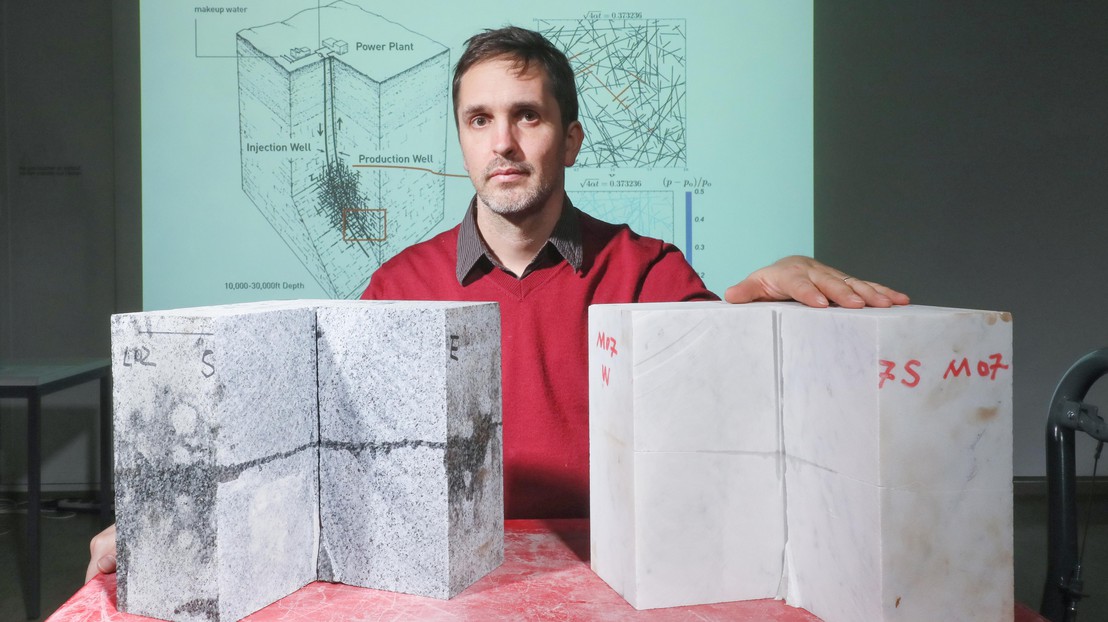
Brice Lecampion is tenure track assistant professor at EPFL. © Alain Herzog/EPFL
Researchers at EPFL have developed a new model to calculate hydraulic fracture propagation. Acclaimed for its accuracy by experts, the model better predicts fracture geometry and the energy cost of hydraulic fracturing – a widely used technique in areas such as CO2 storage, hydrocarbon extraction, dams and volcano hazard monitoring.
Hydraulic fracturing has a wide range of applications, such as improving the productivity of wells used for fluid extraction and injection in porous rock formations. It is a routine part of hydrocarbon extraction but also of deep geothermal power operations, underground CO2 storage and gravity-assisted mining. Engineers use the technique to re-level buildings via compensation grouting, prevent cracks from spreading around dams, and even improve safety in deep underground tunnels. These fractures also occur in nature, such as when magma rises in the earth crust near volcanoes or at glacier beds due to the sudden release of surface meltwater lake.
The industrial process involves the injection of fluid under high-pressure to create cracks in underground rock formations. “There’s a great deal of uncertainty surrounding the effect of turbulent flow when a low-viscosity liquid is used as a fracturing fluid,” says Brice Lecampion, who heads EPFL’s Geo-energy Laboratory (GEL). “We wanted to develop an accurate open-source model that ends this uncertainty once and for all.” Lecampion’s paper, which he co-authored with researcher Haseeb Zia, was published in Journal of Fluid Mechanics in October 2019. In January 2020, this leading journal in the field of fluid mechanics has chosen it for a Focus on Fluids publishing an extended comment of the paper from an expert, in a testament to the relevance of the model developed at EPFL.
Safety and energy cost
In order to inject or produce fluid deep underground, engineers drill a well of about ten centimeters in diameter and often extending two to three kilometers below the surface. Next, they inject a mixture of water and sand into the well over the course of 30 to 45 minutes. This creates a fracture in the rock that can reach up to 500 meters long and 100 meters high. The sand acts as a proppant – a solid material used to keep the fracture open so fluids can flow between the well and the rock. Half of the injected water is typically recovered, filtered and re-injected in subsequent pumping phases, while the other half remains underground.
Engineers need to be able to calculate how these fractures propagate so they can determine precisely how much liquid to inject, and estimate the geometry – or length – of the resulting fractures. Improved estimation of the propagation is also vital to ensure the safety of the process, and helps engineers estimate its energy cost.
The hydraulic fracture process. © iStock
Improving predictions
For shale gas well stimulation, the injected fluid is 99% water. The remaining 1% is a friction reducer additive, a special polymer that drastically reduces turbulent flow by stopping the formation of eddies. The additive, which is widely used in industry, substantially reduces the amount of energy required for high-pressure pumping. Until now, however, its effect on fracture propagation had not been quantified.
“We found that the additive significantly alters fracture propagation under turbulent flow conditions,” explains Lecampion. “Yet the effect only lasts for the first five to six minutes of injection and has little bearing on the final fracture geometry.” The model developed at EPFL allows engineers to more accurately predict the size of the induced fractures and, therefore, how much water can be pumped in and out of the rock, and at what rate. “Very few models of this type are open-source,” adds Lecampion. “The industry is dominated by private firms who tend to keep their calculations and assessments for themselves.”
Emmanuel Detournay, “Slickwater hydraulic fracturing of shales,” Focus on Fluids, January 2020.