Pinewood Makes a Novel Appearance at the Louvre
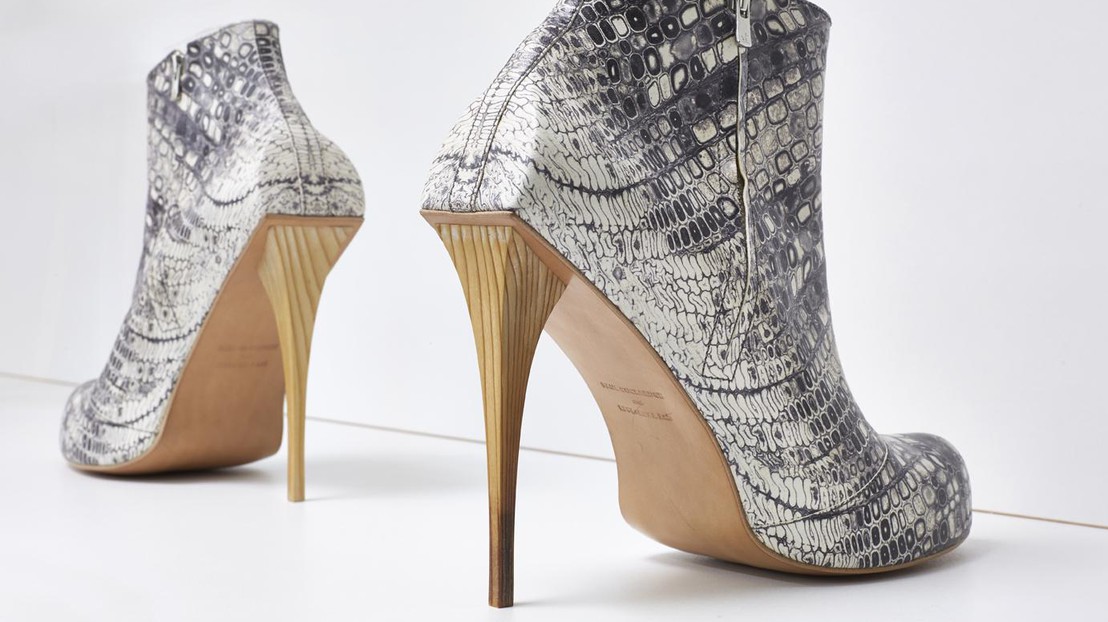
© 2014 EPFL
Start with a soft wood such as pine or fir. Heat it, compress it and turn it into valuable fuel. At the Museum of Decorative Arts in Paris, the EPFL + ECAL Lab presents densified wood objects that show the potential of this material from an EPFL laboratory and highlight the role of design in innovation.
With its texture, hardness and color, one would have to call it tropical hardwood, and yet… Giving a fast-growing soft wood, such as fir, the qualities of a “rare species” is the result of an extensive research project conducted at the Laboratory of Building Materials and the Higher Technical School of Wood in Bienne, under the direction of Parviz Navi. The EPFL + ECAL Lab, whose mission is to use design to explore the potential of new technologies, has taken the results of this work to explore different uses.
From the dialogue between design and science emerges this “new material” heading entering the Museum of Decorative Arts in Paris through the front door. For 6 months, visitors can witness the transformation of a simple piece of fir into real objects. EPFL + ECAL Lab invited five designers to try out this material. Thus was born the heels of Londoner Paul Cocksedge, a doorknob from the studio of Lausanne’s Big-Game, headphones designed by Normal Studio in Paris and romantic boxes by Lea Longis.
A deceptively simple object designed by Chris Kabel surprised engineers with its design complexity. The Dutch designer decided to create a nutcracker of densified wood: “I wanted to use walnut to achieve this cannibalistic idea of a tree that breaks its own fruit!” Doing so required all the scientist’s patience along with the artist’s unfailing hope to give birth to this new material in an everyday object.
These creations come from the same machine used in the scientific research. It enables independent control of the temperature, heat, humidity and pressure of wood placed in a mold. Densifying wood radically changes its structure. Before the process, the tree or other softwood shows a cell structure with a number of tubular cavities. This explains why it is so light and why it floats. In contrast, after densification, the cell walls bond to each other such that there is no more air between the fibers. The material becomes harder and stronger and offers new textures and appearances.
What’s more, the treatment makes it possible to mold the wood into a desired shape. However, the challenges remain substantial. The wood’s complexity, its many natural chemicals, and the sophisticated structure formed by the fibers make densification extremely difficult.
To achieve homogeneous objects, it was necessary to tame the technological reality. Fred Girardet, designer of the machine, conducted dozens of trials before managing to get a perfect piece: “The wood must be constantly monitored. Too hot, too wet, or too small, and the wood splits, browned, and deteriorates. It’s a bit like when you’re baking cookies. The wood’s natural glue interacts with the oven temperature, and when it smells burnt, it's too late!” The work now is focusing on the industrialization process so that densified wood can leave museums and laboratories and be integrated into daily life.