Performance comparison of MEW shape memory polymer structures
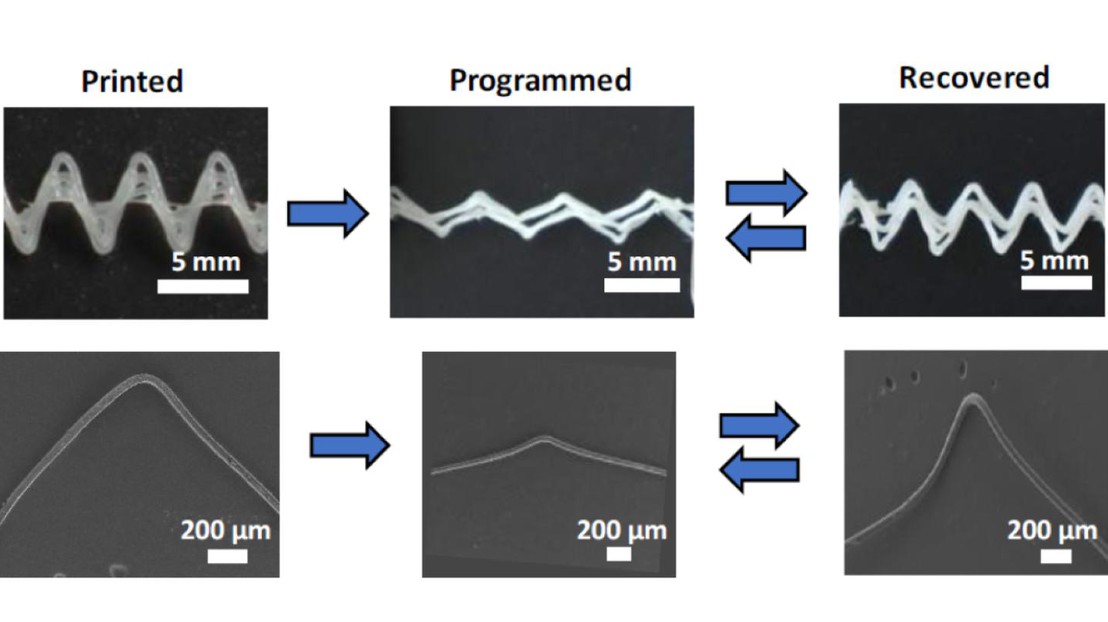
© 2024 EPFL
Congratulations to our colleagues Dr. Biranche Tandon, Reza Farsi, and Taavet Kangur, for their recent publication entitled "Performance comparison of shape memory polymer structures printed by fused deposition modelling and melt electrowriting" in the journal "Advanced Materials Technologies".
Fused deposition modelling (FDM) and melt electrowriting (MEW) are techniques that use polymer fibers as building blocks for printing complex 3D structures, with fibers at the macroscopic and micrometer scale. Here, we use FDM and MEW to produce fibers of shape memory polymer at two different scales, and compare the performance of these fibers, in terms of shape fixity, shape recovery and self-healing properties. FDM and MEW are used for 4D printing a shape memory polymer blend of thermoplastic poly (ε-caprolactone) (30% by wt.) and a soft thermoplastic elastomer polyurethane (70% by wt.) at two different scales. The shape transformation from a programmed temporary state to the printed permanent shape in response to temperature as the stimuli imparts the 4D aspect to the printing. The mean fiber diameter of shape memory polymer produced by FDM and MEW is 340 μm and 40 μm, respectively. The manufactured fibers show excellent shape fixity ratio (~95%) and shape recovery properties (>84%). MEW fibers show a 1.5x faster recovery rate than FDM fibers due to the scaling effect. The excellent shape memory properties are complemented by self-healing characteristics in the printed fibers. Additionally, MEW of a shape memory polymer is directly performed on a cylindrical collector to obtain tubular constructs which could potentially be used as stents for coronary or vascular applications.
For more details, please visit:
N.S. would like to acknowledge the financial support provided to her from UNSW through the PhD research scholarship. X.L. would like to acknowledge the financial support from Australian Research Council (ARC) Discovery Early Career Researcher Award (DECRA) DE190101495. Part of this work has received funding from the European Research Council (ERC) under the European Union's Horizon 2020 research and innovation program (Grant No. ERC-2016-A G, roject “ MEMS 4.0” Grant No. 742685). The authors have no conflict of interests.