Lightweight, ultra-connected seaborne containers
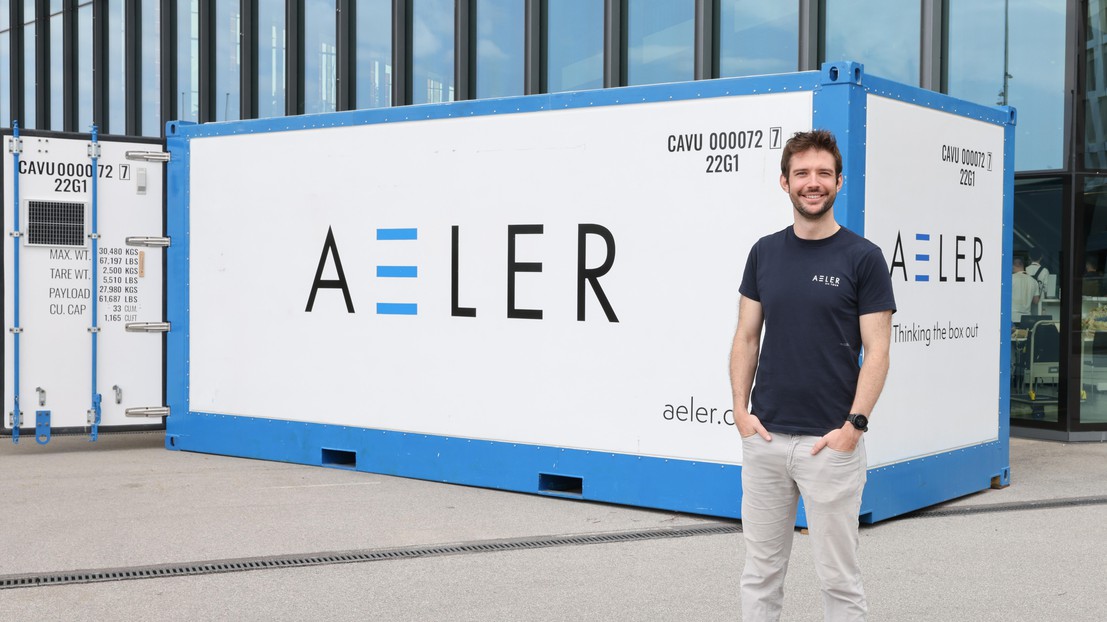
David Baur, cofounder of the start-up © 2022 Alain Herzog
The composite containers developed by AELER, an EPFL startup, deliver better performance across the board: they’re stronger, have a bigger payload, are better insulated, allow for enhanced tracking and can help cut carbon emissions. More than 60 of the containers are currently crossing oceans around the world, and the firm hopes to grow this number substantially starting next year.
Cargo ships carrying containers in a rainbow of colors have been a feature of maritime transport for over 50 years. These containers provide a low-cost, standardized way of shipping goods and are a linchpin of global trade – some 80% of products worldwide are transported via this method. And thanks to the Internet of Things (IoT), shipping containers have gone high-tech in recent years: IoT technology helps lower the financial losses from stolen merchandise, misplaced articles and perishable foodstuffs. AELER has taken these advances one step further with its revolutionary Unit One containers. While these units still meet industry-standard specifications for size, their structure has been improved to provide a bigger payload, greater strength and better insulation. The Unit One design includes a smooth exterior and embedded sensors that send data directly to an application, enabling operators to track goods, monitor shipping conditions and streamline fleet management. The startup raised CHF 7.5 million in an initial funding round and plans to carry out a second one soon. With over 60 Unit One containers already sailing the high seas, the prospects are bright for the young firm to grow rapidly starting next year.
Stronger and better insulated walls

two EPFL professors with whom he worked on the structure
of the containers as an EPFL student © 2022 EPFL© 2022 EPFL
The startup cofounder David Baur, an entrepreneur at heart, has long been convinced of the potential for improving standard metal containers. During his Master’s project at EPFL’s Laboratory for Processing of Advanced Composites (School of engineering), headed by Véronique Michaud, Baur began developing and testing a composite framework made of fiberglass and resin. “When David first spoke to me about his idea, I doubted it could work,” says Michaud. “But his enthusiasm won me over. That wasn’t the first time I’d agreed to a research project that initially seemed a little crazy!” Baur then refined the structure, which resulted in containers that were stronger and much better insulated. With standard metal containers, the wall strength comes from their crenellated structure. But with Baur’s model, the strength comes from the fiberglass and resin composite. That makes his containers lighter and able to carry more goods; they can transport 11% more cargo than a regular refrigerated container and 17% more than containers for liquids. “Because our Unit One containers have such a resistant structure, they don’t bulge under the pressure from liquids,” says Baur. Prof. Michaud is proud of their work. “Our lengthy discussions about the right material have paid off! It’s exciting to see what Baur and his fellow entrepreneurs have done,” she says, patting the huge container.
Moisture-related losses can run into the hundreds of thousands of Swiss francs
We don’t often think about it, but it can get really hot inside metal containers sitting in the sun all day. And the temperature can drop quickly at night. These temperature swings can lead to condensation within the payload, which is problematic for goods like foodstuffs. “Moisture-related losses can run into the hundreds of thousands of Swiss francs,” says Baur. “That’s especially true when the cargo contains pharmaceuticals.” Unit One containers, with their passive insulation, go a long way towards tackling this problem.
The company estimates that its containers can reduce carbon emissions from maritime transport by 20% owing to their bigger payload – meaning fewer containers are needed to ship a given amount of cargo – and smooth, aerodynamic shape. By the same token, when Unit One containers are used on trucks, they can lower the fuel requirement by 4%.
A frontrunner in the logtech industry
Technology has been transforming the field of logistics for several years, giving rise to the portmanteau “logtech.” And here too, the company is breaking new ground. “Our technology is the only one of its kind in the industry, because its embedded devices let operators see exactly what’s going on inside a container,” says Baur. Unit One is opening up new possibilities for connectivity, automation and security. The system’s artificial intelligence programs can make sense out of vast amounts of data so that shipping companies can make faster, better-informed decisions about the optimal routes for their containers. This brings cost savings as well as environmental benefits. AELER’s system also includes an application for tracking input from containers’ embedded sensors as well as a fleet-management program.
The process for manufacturing Unit One containers is more expensive than that for standard metal ones. But the technology offers advantages for the transport of many kinds of goods, from drugs and liquids to luxury goods and personal care products. The startup, founded in 2018, is poised to grab a significant share of the market – millions of containers are currently being used around the world. The company already plans to attend all the major maritime-transport industry conferences this fall. “This is the perfect time for Unit One to hit the market, since the industry is ripe for change,” says Baur.