Les efforts des composites pour virer au vert
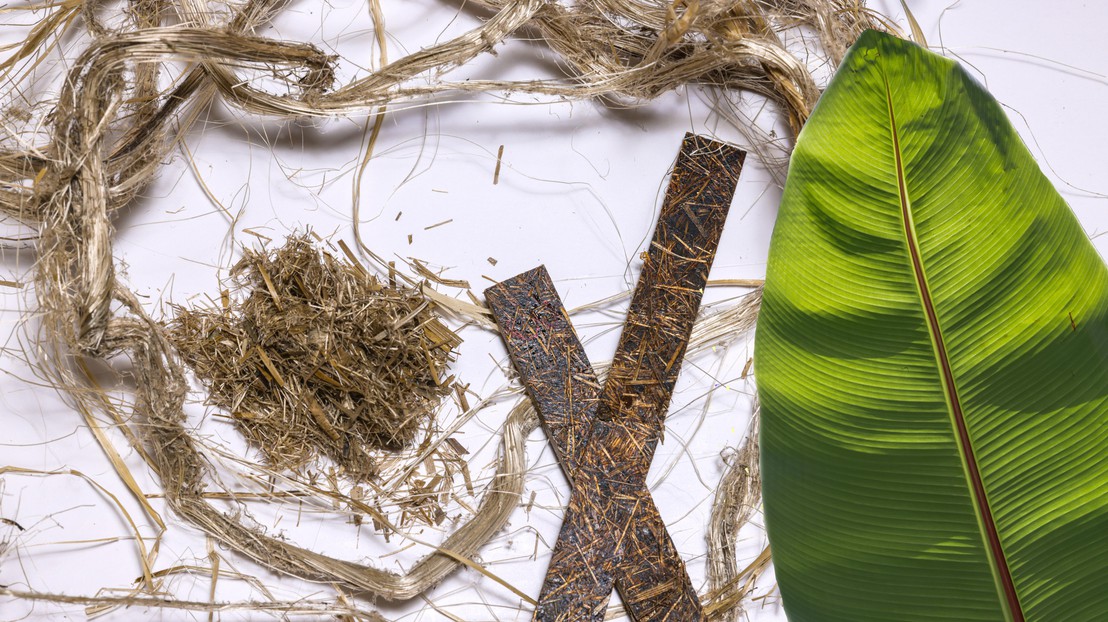
Une piste prometteuse pour certains composites: la fibre de bananiers. 2025 EPFL/Alain Herzog - CC-BY-SA 4.0
Autocicatrisation, autocuisson ou encore réutilisation : de nombreuses pistes pour inclure les matériaux composites dans une économie verte et circulaire se dessinent à l’EPFL et dans ses start-up.
Discrets, légers, résistants à la fatigue et aux intempéries, les matériaux composites se laissent mouler à souhait : ailes d’avion, pales d’éoliennes, cadres de vélo, prothèses médicales ou encore éléments de construction. Leurs qualités singulières excitent les neurones des scientifiques depuis le début du XXe siècle. La perspective d’une substantielle économie de poids, et donc de carburant durant l’essor de l’aéronautique et du spatial dans les années 60, a boosté la recherche, reléguant au second plan la question de l’écologie et du recyclage de ces matériaux qui arrivent aujourd’hui massivement en fin de vie. La prise de conscience sociétale des enjeux environnementaux ces dernières décennies oriente peu à peu les nouvelles générations de matériaux composites vers une économie circulaire. La mise au point de fibres végétales, de résines biosourcées, de procédés de fabrication moins gourmands en énergie et de matériaux réparables guide aujourd’hui les développements scientifiques et technologiques. De nombreuses pistes se dessinent à l’EPFL et dans ses spin-off.
Des matériaux à la fois résistants et remodelables
Les composites tirent leurs propriétés hors normes du mélange de matériaux, un polymère comme matrice combiné avec des réseaux de fibres – le plus souvent en verre ou en carbone –, qui permettent d’optimiser la répartition des contraintes et d’optimiser leurs propriétés mieux que n’importe quel matériau uniforme. Si certaines applications soumises à des conditions extrêmes, comme la structure d’un avion ou d’une fusée, justifient l’utilisation de composés les plus résistants, d’autres remplissent parfaitement leurs fonctions avec des matériaux et des procédés rendant les pièces un peu moins résistantes, mais plus écologiques. L’utilisation de fibres naturelles, comme le lin ou le chanvre, est déjà relativement courante pour certaines parties de bateaux, d’automobiles, ou même de la cabine des avions. « Les recherches des laboratoires incluent maintenant le cycle de vie complet de la pièce composite. Certaines combinaisons de matériaux incluant des fibres de carbone, même si elles sont moins écocompatibles lors de la fabrication, permettent dans le domaine de la mobilité, de faire de grosses économies de carburant durant toute la vie de l’appareil. Les fibres végétales sont très intéressantes car de source renouvelable, mais il faut prendre en compte les pesticides, l’engrais ou encore l’eau nécessaires aux cultures. Une piste prometteuse pour un bilan encore meilleur est la fibre de bananiers par exemple, qui représente un déchet de l’agriculture puisque les plants sont de toute façon arrachés tous les trois ans par les cultivateurs », souligne Véronique Michaud, professeure au Laboratoire de mise en œuvre des composites à haute performance (LPAC) à la Faculté des sciences et techniques de l'ingénieur de l’EPFL.
Les recherches des laboratoires incluent maintenant le cycle de vie complet de la pièce composite.
Les résines, fabriquées majoritairement à base de sous-produits pétroliers, sont souvent pointées du doigt pour leur impact environnemental. Des alternatives biosourcées sont progressivement explorées par les chimistes et souvent incluses pour un certain pourcentage dans les polymères. Mais la petite révolution sur laquelle se penchent de nombreux laboratoires actuellement est un nouveau type de résine dite vitrimère. Voilà plusieurs décennies que les scientifiques tentaient de trouver le matériau capable de concilier les propriétés des deux types de polymères usuels : l’un très résistant, mais difficile à recycler, l’autre plus facile à transformer et à revaloriser, mais souvent moins performant. « Les vitrimères ouvrent de formidables possibilités, confirme la professeure. Dans le cadre du projet ZeroPol financé par Innosuisse, qui vise à minimiser l'empreinte CO2 des produits plastiques tout au long de leur cycle de vie, nous testons par exemple diverses compositions développées par une grande entreprise bâloise afin de les appliquer aux composites, fabriquer des pièces et en évaluer les propriétés. » Un projet européen auquel participe également le LPAC vise à mettre au point une formule de résine vitrimère relativement souple qui puisse être remodelée en la chauffant légèrement, destinée, par exemple, à des écouteurs.
Un matériau qui autocuit pour décarboner la fabrication
Le bilan carbone des composites à haute performance souffre également de procédés de production très gourmands en énergie. Afin d’assurer une qualité maximale, le procédé habituel pour les composites à haute performance passe souvent par une cuisson en autoclave, sorte de cocotte-minute géante. « Près de 95% de l’énergie sert à porter l’appareil lui-même à la bonne température », constate Véronique Michaud. Pour parer à cette débauche d’énergie, les scientifiques du LPAC développent une résine qui autocuit. « L’idée est d’allumer un coin de la pièce en composite avec une lumière UV, puis de laisser la chaleur se propager toute seule grâce à l’agencement de la structure moléculaire du matériau ». Le procédé fonctionne sur des échantillons, mais nécessite encore quelques années de recherche afin de le maîtriser et pouvoir le reproduire à grande échelle. Des méthodes pour se passer de l’autoclave, issues de ce laboratoire, ont déjà largement fait leurs preuves puisque, mis au point pour élaborer la coque du bateau Alinghi au début des années 2000, un procédé analogue est utilisé par l’entreprise Beyond Gravity (anciennement Ruag Space), près de Lucerne, pour fabriquer les coiffes des fusées Ariane.
De l’autoréparation à la fibre intelligente
Très résistants, les matériaux composites ne sont cependant pas à l’abri de chocs qui altèrent leur structure. Il y a donc un intérêt croissant, à la fois dans la recherche académique et l’industrie, pour les matériaux composites autocicatrisants afin d’allonger encore leur durée de vie. Lorsqu’une bosse ou une fissure de surface apparait, des agents d’autoréparation inclus dans la composition chimique sont libérés. Le spin-off CompPair développe par exemple des résines qui permettent une réparation de l’objet en chauffant l’endroit abimé à une centaine de degrés. Mais le point faible des dispositifs en composite réside parfois davantage dans la juxtaposition des pièces que dans les avaries du matériau lui-même. C’est notamment le cas des pales d’éoliennes pour lesquelles le LPAC collabore avec le Groupe de mécanique des composites de l’EPFL pour développer une colle dotée de microparticules polymères qui lui donnent une consistance idéale de pâte et permettent une réparation par chauffage lorsqu’une fissure apparait. Finalement, glisser des fibres intelligentes à l’intérieur des structures permettrait d’obtenir des informations du cœur de la pièce pour décider du besoin de réparation ou de mise au rebut. Le Laboratoire des fibres et matériaux photoniques, piloté par Fabien Sorin, spécialiste des fibres intelligentes, collabore avec le LPAC sur plusieurs projets visant à intégrer de tels capteurs dans les pièces composites.
Que faire des composites en fin de vie?
L’étroite imbrication de matériaux, qui fait la force des composites durant leur utilisation, se mue en point faible au moment du recyclage. La majorité des composites de première génération, qui arrive aujourd’hui en fin de vie, est brûlée ou enfouie, car les matériaux utilisés ne sont plus d’actualité. Cependant des projets de génie civil et architecturaux réutilisant des structures en matériaux composites commencent à émerger. « Cela reste un débouché de niche, mais qui pourrait être bien plus répandu qu’il ne l’est actuellement », souligne Anastasios Vassilopoulos, professeur dans le Groupe de mécanique des composites. « Nous avons, avec Clemens Waldhart, architecte chargé de cours au Laboratoire d'architecture élémentaire et études de types, réalisé plusieurs projets pour réutiliser des pales d’éoliennes comme structures de bâtiments (photo1) ou pour couvrir l’autoroute de contournement de Lausanne Sud et y placer des panneaux solaires (photo2) . Les deux projets sont en cours de développement et à la recherche d'un soutien suffisant de la part des différents acteurs concernés.»

2025 AFF/AFFECT/EPFL EAST -CC-BY-SA 4.0
Finalement, des méthodes qui permettent de récupérer séparément les fibres et la résine afin de les recycler vers de nouveaux composites existent, comme la pyrolyse – un chauffage à très haute température – ou l’utilisation de solvants. Plusieurs entreprises, dont Composite Recycling ou Verretex de l’EPFL, tentent de rendre ces procédés écologiques et économiquement rentables. La première mise sur un dispositif ambulant permettant de traiter les éléments de bateau directement à proximité du port. L’objectif est d’obtenir des morceaux de fibres recyclées suffisamment longs, qui puissent être réutilisés sans avoir besoin de les faire fondre. Verretex développe une technologie permettant d’obtenir des assemblages de fibres courtes, non tissées, et disposées en vrac d’une qualité identique aux originales.
