“Hardly a day goes by that I don't build something”
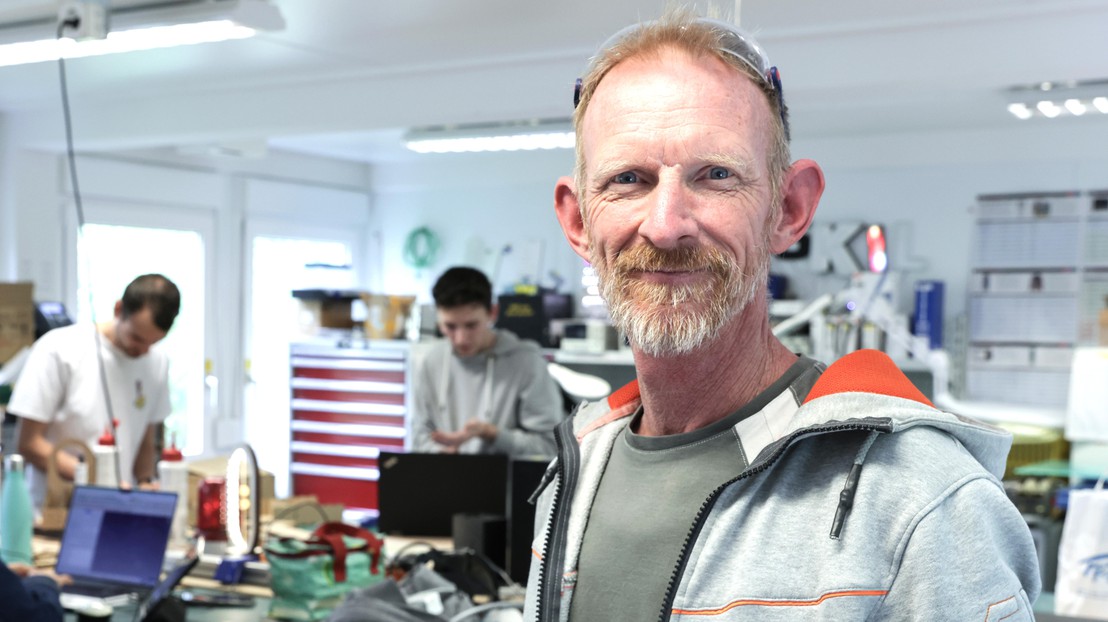
© 2024 EPFL/Alain Herzog - CC-BY-SA 4.0
Over two decades ago, Stéphane Clerc started getting involved in the technical work behind some high-profile projects involving EPFL – including Alinghi and Solar Impulse. For the past six years, he’s been drawing on that experience as a coach at EPFL’s SKIL workshops.
At EPFL’s Student Kreativity and Innovation Laboratory (SKIL), students saw, glue, shape and assemble pieces of wood and cardboard to create their inventive prototypes. The workshops they use are housed in three stacked shipping containers and fitted out with digital machines and 3D printers. That’s where Stéphane Clerc coaches the students, encouraging them and nurturing their creative spirit. “My job is to teach students to work with their hands,” he says. “I help them link theory to practice and learn about different materials, ways of designing prototypes and how to manage projects.”

Clerc works alongside two other SKIL coaches who also bring solid experience: Stéphane Pilloud, a former boat-maker and beekeeper, and Marc Wettstein, a globe-trotter who has crisscrossed the planet to cover major events and conflicts. “We’re there to guide the students and make sure they think things through, but also to hold them back when necessary,” says Clerc. “We like to say that the three of us together have over 100 years of experience!”

From wood to carbon fiber
A cabinetmaker by training, Clerc completed his apprenticeship in Switzerland – a dream opportunity with a very determined boss. “His Swiss federal certification at the time was only provisional, although the government agreed to make an exception so he could hire me as an apprentice,” says Clerc. “And one condition for him to obtain his permanent certification was for me to pass my apprenticeship. So as you can imagine, he watched me like a hawk! It was four years of being drilled like crazy by my supervisor.”
A few years later, Clerc opted for a career change, driven partly by his curious nature – he wanted to explore other fields – and partly by his love of mountain sports. He decided to join Nidecker, a snowboard manufacturer based in Rolle, where he helped develop prototypes and try out new materials.

Clerc later took a position at Décision SA, a producer of composite materials. “I was involved in creating hundreds and hundreds of prototypes during my 22 years at Décision, working on projects spanning an array of industries: shipbuilding, aerospace, aeronautics, automotive, sports, construction and more,” he says. “I had the chance to work on different boat designs for Alinghi, which won the America’s Cup in Auckland in 2003 and Valence in 2007. I was also on the maintenance team at Valence, repairing and adjusting the boat as needed.”

Solar Impulse, an ambitious project
Then Clerc found out about the Solar Impulse project. The CEO of Décision – Bertrand Cardis – was a longtime friend of an airplane pilot named André Borschberg. They were fellow EPFL graduates too. At the time, Borschberg was working with Bertrand Piccard, who had just completed a trip around the world in a hot-air balloon, to design a carbon-fiber aircraft powered entirely by solar energy. Their idea was to make another trip around the world – but this time, without the use of fossil fuels. An incredibly courageous venture.

Clerc recalls: “We started completely from scratch. There were around 15 of us on the project, some of whom had never touched carbon fiber before. We had to do everything ourselves – create the molds and find the right kind of glue, for example – and design everything by hand: the aircraft’s 2,500 carbon-fiber parts as well as all the other components. In the end, there were around 6,000 parts. Each one was a prototype, but they all had to be tested and certified suitable for flight."

©Creative Commons
The aircraft presented other colossal challenges as well, such as installing and encapsulating the 11,628 photovoltaic cells needed to cover the aircraft’s 63 meter-long wingspan. After four years of non-stop work, Solar Impulse was ready for test flights. “It was an intense period,” says Clerc. “I came home in the evening and kept on working. The project haunted my dreams and nightmares for ten years. Today, it features prominently on my CV. I’ve kept some of the parts I made – and still wear the T-shirts!” When EPFL introduced the SKIL initiative, Clerc felt it would be a good way for him to share his experience.

Now he’s a SKIL coach during the week and a handyman on weekends and during school breaks. “Hardly a day goes by that I don’t build something, whether for me, a friend or a neighbor,” he says. During the pandemic, the neighborhood kids often hung out at his home workshop: “It was like a mini-SKIL, but for children. Then their parents started coming too, they had the time. By the time the pandemic was over, people had gotten into the habit of stopping by. So I still spend my free time repairing and restoring things and giving them tips.”
