Experts revive ancient techniques to make concrete more sustainable
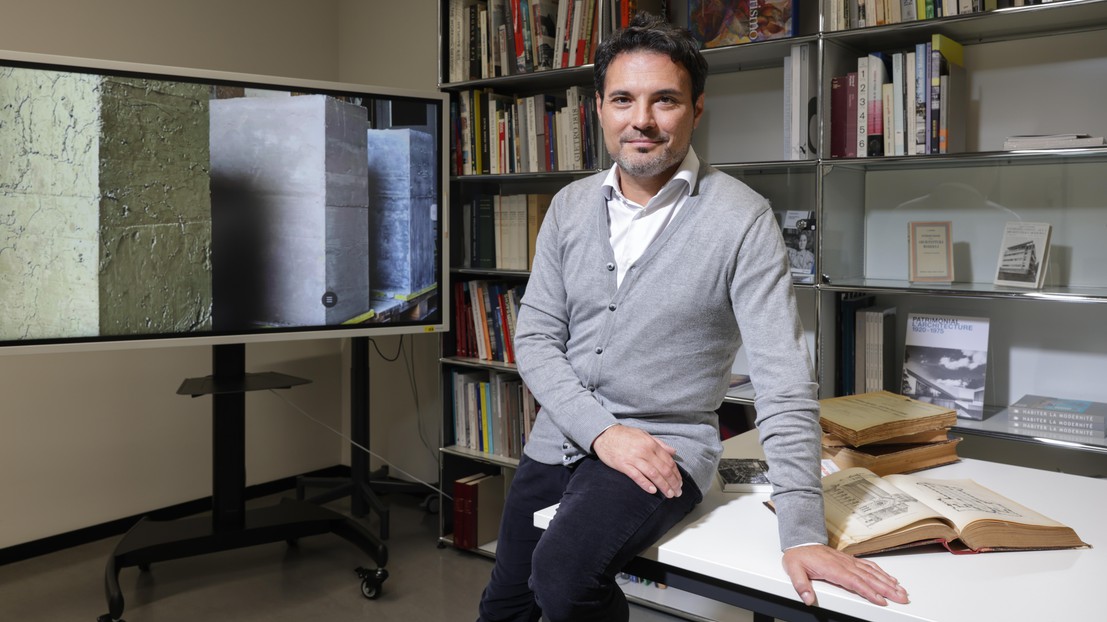
Salvatore Aprea, between archives and projection of wall prototypes. © 2023 EPFL / A. Herzog-CC-BY-SA 4.0.
A team of experts from EPFL, ETH Zurich and a Geneva-based architecture firm has developed a new type of non-reinforced concrete made from stone offcuts. Their method, which reduces the use of carbon-intensive cement-based binders, draws on ancient techniques uncovered in historical archives.
Some walls could easily be built without reinforced concrete, a material that accounts for a large share of the construction industry’s carbon footprint. In fact, these walls could even be made from unprocessed quarry waste. To see how this might be possible, the research team – consisting of experts from EPFL’s Archives of Modern Construction (Acm) research group, the ETH Zurich Chair of Sustainable Construction, and Archiplein – delved into historical archives to unearth forgotten construction methods. They tested various options involving different processes and cement mixtures as part of the Circular Building Industry (CBI) Booster, a program that backs innovative construction-industry initiatives based on circular principles.
Towards the end of October, the team built six load-bearing walls in Lucery-Villars, in Vaud Canton, using recovered stone-quarry waste and fieldstone. They divided their prototype structures into two groups so that they could test two different construction methods and three types of mortar-based binders. The first method involved placing the mortar in the formwork before adding the stones, while in the second method, the order was reversed: the stones were first laid in place and then coated with mortar. Of the three binders tested by the team, one contained a small quantity of cement, another was a lime-based mixture, and the third was made from infertile soil. Given the sheer size of many of the stones used to make the walls, the experts named their method “Cyclopean” in reference to a type of stonework found in early architecture.

Upcycled waste materials
At present, stone-quarry waste is processed before being reused, which consumes large amounts of energy. And producing cement – the binder used in concrete – is an even more energy-intensive process: limestone is heated to 1,450°C in permanently operating rotary kilns. There’s also another problem: concrete is made from inert materials, and the available options are limited. “For centuries, builders tried to cut costs by limiting how much cement they used and incorporating recycled waste materials into their concrete,” says Salvatore Aprea, head of the Acm research group. “The challenge now is to revive these old methods – not for financial reasons but for the sake of our planet.” For Marlène Leroux, a partner at Archiplein, the current state of play is nothing short of baffling: “We seem to have forgotten how to build simple load-bearing walls from stone offcuts, with a minimal carbon footprint and without the need for additives, chemicals or steel reinforcement bars.”

From Roman times to the 19th century
To gain inspiration for the project, the Acm group combed through technical archives dating from Roman times through to the 18th and 19th centuries – mostly from France and Germany – in search of old concrete and cement formulas. They looked specifically for methods that would allow them to use both unprocessed stone offcuts and mortars containing little to no cement. “We found detailed experimental results where engineers had tested the strength of mortars with different lime concentrations,” says Aprea. “In most cases, these mortars were made from materials sourced locally or nearby.” The experts also studied early concrete-application methods. Prof. Guillaume Habert, who holds the ETH Zurich Chair, worked with Leroux and two of her colleagues at Archiplein – architect Francis Jacquier and engineer Olivier Dahenne – to develop computer models for identifying new mortar formulas inspired by the past but fit for modern specifications.
Following this initial research, the team’s next step will be to develop standardized, mechanized, low-carbon wall construction methods. They plan to build prototypes, run strength tests and produce comparative tables, much in the same way as engineers and scholars of the past like Louis-Joseph Vicat, Jean Henri Hassenfratz and John Smeaton, whose work they examined in detail for this project.
Circular Building Industry Booster (CBI)
Projet Circular Buildling Industry Booster: «Le Béton Cyclopéen ou comment s'inscrire dans le continuum des savoir-faire constructifs à l'aune des problématiques climatiques et environnementales», Marlène Leroux (co-funder), Guillaume Habert (Associate Professor at the Chair of Sustainable Construction, ETH Zurich), Francis Jacquier (architect), Salvatore Aprea (Director, ACM Group), Olivier Dahenne (engineer), October 2023.