EPFL now has its own Hyperloop test track
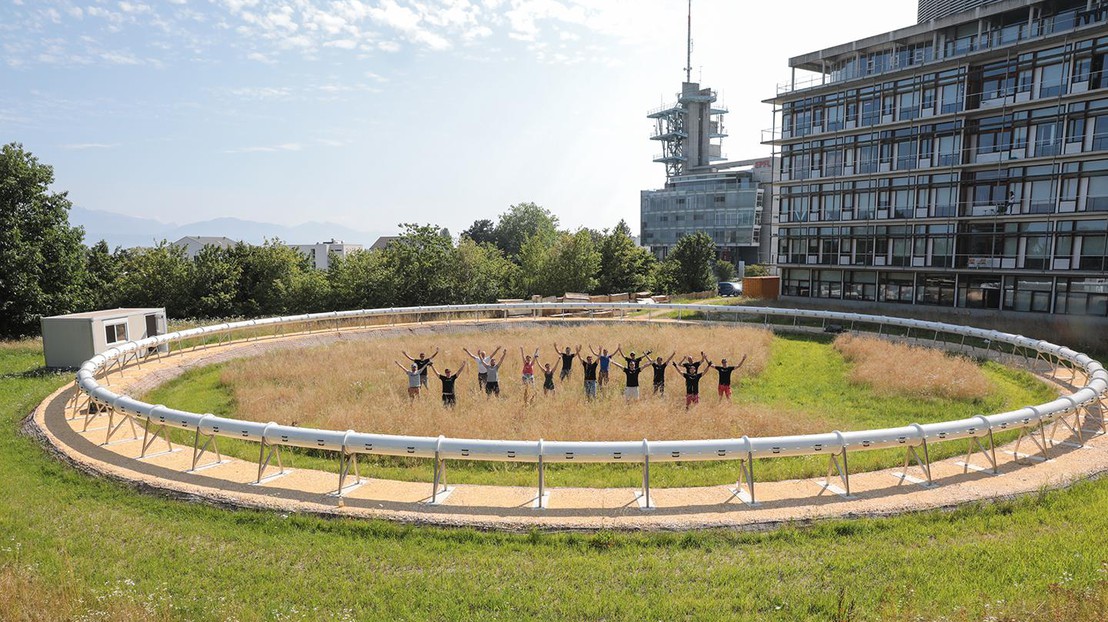
The test track – 40 m in diameter and 120 m long – is a first in Europe. © Murielle Gerber/EPFL
Engineers at EPFL’s DESL lab, working in association with EPFL spin-off Swisspod, have built a Hyperloop test track on the Lausanne campus. They will use the loop – a large vacuum tube for ultra-high-speed travel – to test a linear induction motor. The research is being funded by an Innosuisse grant.
Hyperloops, viewed by some as the fifth mode of transport, stand to revolutionize long-distance travel. They offer a cleaner alternative to planes and are faster than trains. Hyperloop projects are already under way in the Nevada desert, Port of Hamburg, Toulouse, the Near East and China. And yesterday, a team of engineers from EPFL and Swisspod unveiled a circular test track on the Lausanne campus – Europe’s first operational model Hyperloop. It will be used to study new ideas for the loop’s structure and pod and assess its viability for ultra-high-speed mass transportation.
The test track – 40 m in diameter and 120 m long – was developed by School of Engineering’s Distributed Electrical Systems Laboratory (DESL), headed by Mario Paolone. It’s made out of aluminum alloy and designed to simulate an infinitely long Hyperloop, with pods of various sizes depending on the testing objectives and results. Its performance in terms of the propulsion and levitation system and kinematics will be tested under vacuum at a scale of 1:6. Its numerous high-tech sensors will give engineers key information about their design’s properties. “With this reduced-scale test track, we will be able to study the fundamental aspects of our pod’s electromagnetic propulsion and levitation system,” says Paolone. “We’ll use the results to enhance the pod design and make the loop operate more efficiently.”
With this reduced-scale test track, we will be able to study the fundamental aspects of our pod’s electromagnetic propulsion and levitation system. We’ll use the results to enhance the pod design and make the loop operate more efficiently.
The pod’s components were produced using DESL’s industrial-scale 3D printer, which can fabricate objects up to 45 cm in size in a range of materials (such as ABS, PLA, PET, nylon, carbon, Flex, polystyrene and Laywood). Special software will be used to replicate the power grid’s behavior in real time, like a digital twin.
Cutting power use with a linear induction motor
One of the big challenges of a Hyperloop is its propulsion system. To keep costs down, the energy required for propulsion in the EPFL design will not come from the track – as it does for Maglev trains – but will be carried by the pods themselves. They will be equipped with linear induction motors, although further development work is needed to reduce the pods’ power consumption. The target is to reach a power consumption of 10–50 Wh/km per passenger (depending on how long the trip is), compared with 97–100 Wh/km for electric cars and 515–600 Wh/km for planes. The development work will be carried out under the LIMITLESS project (for Linear Induction Motor drIve for Traction and LEvitation in Sustainable hyperloop Systems) involving Swisspod, DESL and the Vaud School of Management and Engineering (HEIG-VD), with the support of an Innosuisse grant. Once the low-power linear induction motor is ready, it will be tested on the EPFL track.
“This project provides a great opportunity for Swisspod to join forces with EPFL’s world-class engineering skills,” says Denis Tudor, CEO of Swisspod and a PhD student at EPFL. “By combining those skills with our own business and engineering capabilities, we hope to develop a system that will reach the market in four to five years.” Georgios Sarantakos, who heads up the project at DESL, adds: “Both DESL and Swisspod aim to use innovation as a vector for positive change and develop a feasible transportation system that can bring real value to the local community and deliver significant benefits to society as a whole.”
Close to 20 students from various EPFL schools are taking part in EPFLoop as part of their semester or Master’s projects. “In prior years, our main goal was to break speed records at international Hyperloop competitions,” says Georgios Sarantakos, the project head at DESL. “But now we want to define certain parameters and improve efficiency so that one day we can build a full-scale track.” Meeting that goal will require pushing the boundaries of technology in a range of areas, including batteries, power electronics, propulsion systems, heat management, avionics, design, tubular structures and data management.