Democratising robotics with artificial intelligence
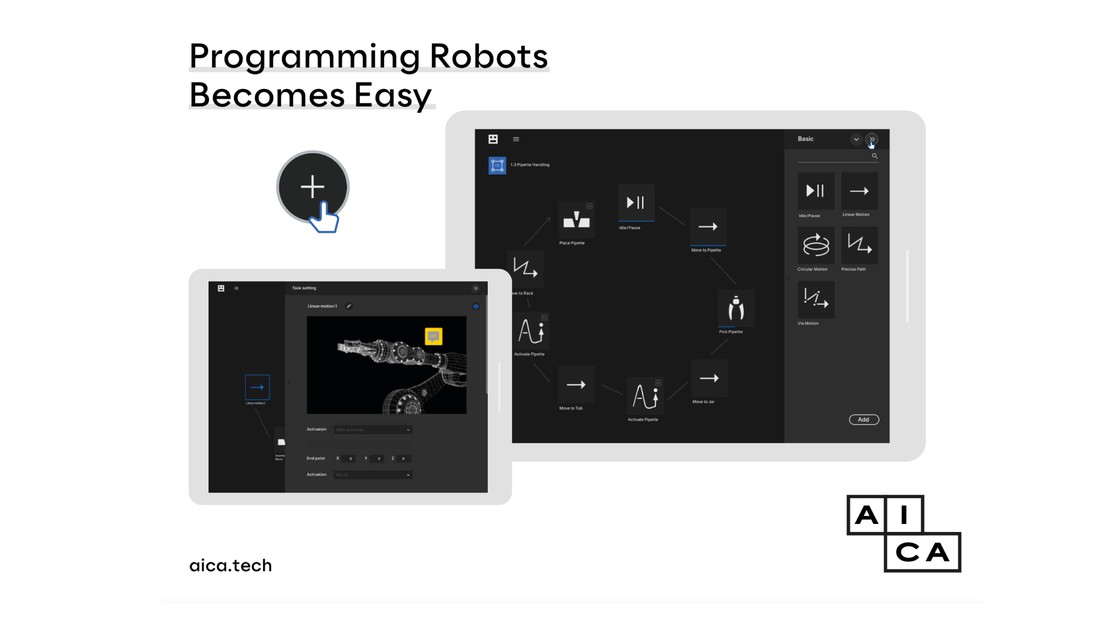
© 2021 EPFL EPFL - Alain Herzog
The difficulty of programming robots makes the technology inaccessible to many companies, especially the small batch manufacturers that define Swiss industry. AICA, a new AI-driven software co-founded by Professor Aude Billard, Lukas Huber, and Dr. Baptiste Busch, aims to change that.
Robotics are the future of manufacturing. Robots continue to grow faster, smarter, and more useful. According to reports, the global robotic market is currently worth around US$115b. This is expected to grow to over $275B in the next five years. In Switzerland alone, more than 2,000 new robots are installed every year.
While robots can be used across manufacturing, currently only around 75% of tasks in factories are automated. Many smaller manufacturers can’t take advantage of this technology at all, thanks to the investment needed. Aside from the cost of the robot itself, each time the robot does something new, it needs to be reprogrammed. This can cause a week’s downtime, and requires specialist programming expertise - even small, standard changes. For businesses which work with small batches of product or complex tasks, such watchmaking or medical devices, automation, and the cost, just isn’t worth it.
AICA, co-founded by Professor Aude Billard from the School of Engineering, Lukas Huber and Dr. Baptiste Busch, aims to change that by simplifying robot programming with a new software interface.
First off, can you tell us a bit about how robots are used in manufacturing?
Baptiste: When we think about robotics, we imagine the automotive industry, where you have big industrial lines full of robots that do every task with little to no variation between the cars. But robotics can have a bigger impact in industries that have very small batches of product or complex tasks, like watchmaking or medical, for example. In these industries, however, it is currently expensive to use robots. That’s the challenge we’re trying to address.
Why is using robots so expensive for small batch manufacturers?
Baptiste: Every time you change a task, the robot needs to be programmed and you need to call an expert. If you have frequent changes, it becomes very expensive. Manufacturers that produce either small batches or batches that change often need to reprogram the robot for every batch, which adds up quickly.
Lukas: This reprogramming has an impact on downtime – and that costs money. The reprogramming can take up to a week, during which your production stops. So you’ve got the working costs of the integrator (which can easily cost between 5,000 and 10,000 swiss francs) plus the cost of stopping production for a week. With AICA, we can reduce this week of programming just to half a day.
How does AICA work?
Lukas: We like to think of AICA as a new brain for the robot. Everything is in this little box, which the user simply plugs in. They can then interact with the robot through a simple software program. The software uses drag and drop modules – these can be super simple or more complex, depending on the task. For example, a task like inserting a screw is easy for a human, but is almost impossible to program for a robot. So, we have developed an algorithm where we can either show the robot how to do it, or the robot can learn to do it itself. As a result, we’re opening up the scope of tasks robots can do - tasks that were almost inaccessible to industry before.
Baptiste: We wanted to make it super simple to program robots and for them to learn new tasks. We use a simple graphical interface, so if you know how to use a smartphone or tablet, then you should be able to use our software.
You’ve recently started working with a designer. What’s the value of design to a startup like yours?
Lukas: Yes, not only did we feel it was important to get a professional logo, website, and corporate identity, but having a designer has really helped us with the design of the front-end interface of AICA.
Baptiste: I was surprised at how much expertise the designer bought to something I thought would be quite simple. The designer looked at how the interface would be used by our customers, the journey they would need to take, and how to make the technology even easier to use.
Lukas: We’re bringing a completely new solution to the market. It’s crucial that the user experience is simple. Thanks to our collaboration with a designer, we’ve managed to hide incredibly complex artificial intelligence algorithms behind a friendly and easy to use interface. This kind of customer experience knowledge is vital for all startups.
What’s next for AICA? How will you use your Innogrant?
Lukas: For the past half a year or so, we’ve been talking to partners and potential clients. There is a lot of interest in this software, and we now know we can add value to their production.
The Innogrant will help us focus on the first projects with industrial partners so we can prove the concept and scale up from a small laboratory project to something that is useful in the real world. We’ve spent the time on the research and have these deep algorithms, so now it’s about finding industrial partners and making the software easy for them to use and adapting the algorithms to their industry.
After that, we will focus on having a global impact. In order to scale we’ll need a bigger team and the support of an investor to realise the potential of our technology
AICA is based in the Learning Algorithms and Systems Laboratory (LASA) under the supervision of Dr. Aude Billard, professor and head of LASA, specialized in Artificial Intelligence, Collaborative Robotics and Human Robot Interaction. Find out more at aica.tech.
For more information on Innogrants and details on how to apply, visit the Startup Unit website.