Control of molecular motion by metal-plated 3D-printed plastic pieces
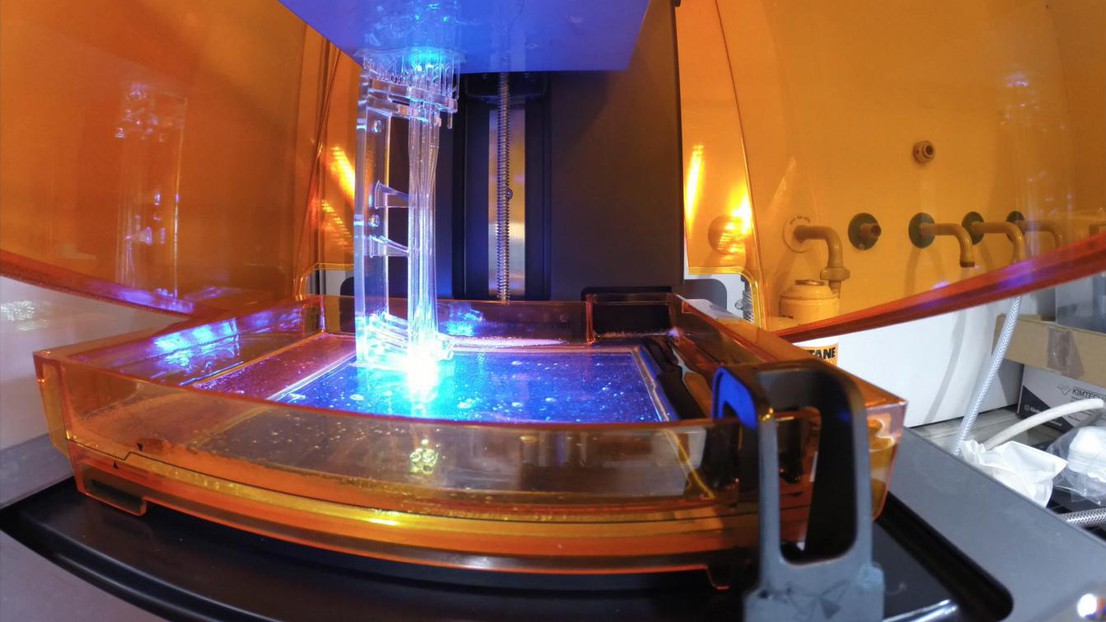
The 3D printer used in this study © A. Osterwalder/EPFL
EPFL scientists have combined 3D-printing with electroplating to easily produce high-quality metal electrodes that can be used as a molecular beam-splitter.
Many measurement techniques, such as spectroscopy, benefit from the ability to split a single beam of light into two in order to measure changes in one of them. The crucial device that separates the beam is the beam-splitter. These have been mostly limited to light beams, where one uses simply a partially reflective glass. EPFL scientists have now developed a similar device for splitting beams of molecules, where high-voltage electrodes are used to control the motion of the molecules inside a vacuum. The electrodes are built by an innovative method that combines 3D printing and electroplating for the fabrication of complex metallic structures. The same approach can also be used in a wide range of other experiments. The new method is published in Physical Review Applied and overcomes previous fabrication problems thus opening up new avenues.
Sean Gordon and Andreas Osterwalder at EPFL’s Institute of Chemical Sciences and Engineering, developed the new fabrication method, and demonstrated it by constructing the complicated combination of electrodes required to guide and split beams of molecules. The production method not only allows complex shapes to be made but, in addition, speeds up production by a factor of 50-100.
The technique begins by 3D-printing a plastic piece and then electroplating a 10 μm-thick metal layer onto it. Electroplating is an established technique in various branches of industry like the automobile industry, fabrication of jewelry, or plumbing. It generally uses electrolysis to coat a conductive material with a metallic layer. “but the plating of printed pieces has not been done before in the context of scientific applications,” says Andreas Osterwalder.
To make the printed plastic pieces conductive and thus amenable to electroplating, they were first pre-treated by a special procedure developed by the company Galvotec near Zurich. Once the first conductive layer was applied, the pieces could be treated as if they were metallic. The first step can be applied selectively to certain regions of the printed piece, so that the final device contains some areas that are metallic and conductive while others remain insulating.
This process enabled the researchers to build two electrically independent high-voltage electrodes from a single printed plastic piece and with the correct geometry for beam-splitting. Meanwhile, the procedure allows an almost free choice of the coating metal, including some that would be very hard to machine.
The completed electrodes (credit: A. Osterwalder/EPFL)
This approach also produced surfaces that have no scratches, recesses or abrasions. The molecular beam-splitter used to prove the new method is a structure based on very complex electrodes that require impeccable surface properties and high-precision alignment. “All of which comes for free when using the 3D-printing approach,” says Andreas Osterwalder.
Along with cost, the new 3D printing/electroplating method also drastically reduces production time: Traditional manufacturing for such structures can often take several months. But in the EPFL study, all the components were printed within 48 hours and electroplating only took a day. The shorter time allows for very fast turnover and more flexibility in the development and testing of new components.
Finally, 3D printing uses an entirely digital workflow — the electrodes are printed directly from a computer and require no manual input. This means that an exact replica of a complete experimental setup can be reproduced anywhere by simply transferring a computer file.
The new fabrication method highlights the enormous potential that 3D printers have for fundamental research, in a variety of research areas. It especially demonstrates that we can now quickly produce chemically robust electrically conductive pieces with high precision and at low cost since 3D printing is virtually unlimited in terms of design and the geometry of structures.
This work was funded by EPFL and the Swiss National Science Foundation (SNSF).
Reference
Sean D. S. Gordon, Andreas Osterwalder. 3D printed beam splitter for polar neutral molecules.Physical Review Applied 27 April 2017. DOI: 10.1103/PhysRevApplied.7.044022