Concrete Developed at EPFL to Rescue Brittany's Lighthouses
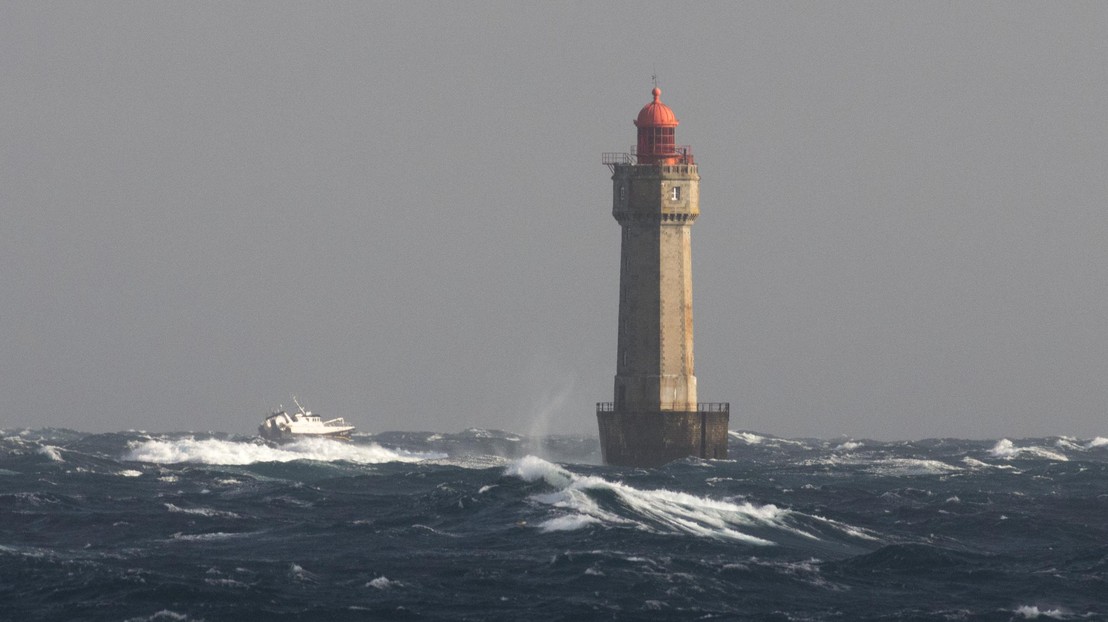
© 2013 EPFL Emmanuel Denarié
A lighthouse turret off the coast of Lorient in Brittany has been enhanced with technology developed at EPFL for bridges. This trial run will test the application of Ultra-High Performance Concrete (UHPC).
They are nicknamed hell, purgatory or heaven after they are built at sea, clinging to an islet or built on land. Some famous lighthouses of Brittany, like the Jument or Ar-Men, have stood at the intersection of violent currents, blinding storms and breaking surf for over a century. The repeated attack of waves on the bases and towers renders them fragile. Despite the reinforcements made through the years, they inevitably deteriorate under the constant onslaught of the sea.
Thus far “bandages” of reinforced concrete have been applied at the foot of these structures, but they always eventually deteriorate. The Centre for Maritime and Fluvial Studies (CETMEF) in Brest, which oversees the management of such marine construction, has accepted the proposal of EPFL engineers, in partnership with Lafarge, to develop the application of high-performance concrete cast in situ to stop the destruction of these honorable sentries.
Waterproof concrete
The Ultra-High Performance Fiber-Reinforced Concrete is a mixture of cementing materials – identical to what is found in most modern concrete – and steel fibers. This choice, based on chemical analysis and particle size, makes it both exceptionally compact and waterproof. Its fibers give it a deformation capacity comparable to that of the steel without the weight or corrosion sensitivity. Its impermeability is such that even when deployed in a thin layer, water and salts are unable to attack.
At the same density as concrete, a thin layer of merely a few centimeters suffices to protect the structure. “With traditional concrete a thickness of 6-7 cm is required to protect a metal frame. With UHPC 15 mm is sufficient and even achieves much greater durability,” says project head Emmanuel Denarié.
To the rescue of existing structures on land and at sea
The forebears of UHPC appeared in 70-80 AD and were mostly used in prefabrication. Since 2004 the Laboratory of Maintenance, Building and Construction Safety (MCS) has played a pioneering role in the application of these materials cast on existing structures – under increasingly demanding conditions. They create a veritable second skin that protects and strengthens. This technology has become common in Switzerland. “For lighthouses the problem is very similar to that of bridges. The duration of intervention should be minimized; we must propose extremely efficient and durable construction solutions using minimal materials. Therefore, it was natural to advise this technique to our French colleagues,” says the researcher.
Greener materials
MCS is now one of the most advanced laboratories in the world in the understanding of UHPC and its application for the improvement of existing structures. It has applied its skills to service many bridges in Switzerland and abroad. Also MCS has developed new techniques using increasing materials that are green and regional. “The traditional matrix of UHPC uses a lot of cement. Our research has proven that only 40% of it is necessary to obtain high performance concrete suitable for reinforcing structures. We therefore developed greener UHPC matrices by replacing mass cement primarily with limestone powder,” says Emmanuel Denarié.
The laboratory now has 10 years of insight into the behavior of UHPC on the many structures it has reinforced or preserved, such as the bridge over the Morges in Valais, the Bridge Log Čezsoški in Slovenia, or even the fire station in Geneva. “At most we found marks of surface corrosion but absolutely nothing in depth.” The tests on structural elements clearly show the total impermeability of UHPC under actual operating conditions.
This new approach surely represents a glimmer of hope for the old lighthouses of the West Atlantic.