Chip lets scientists study biocement formation in real-time
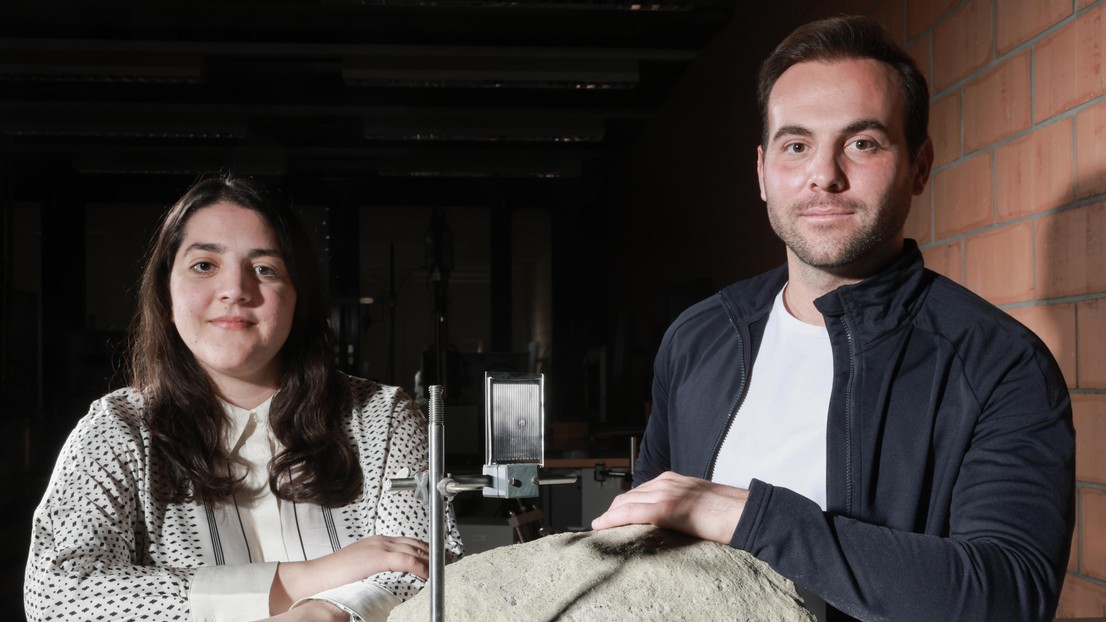
Ariadni Elmaloglou, PhD student, and Dimitrios Terzis,one of her thesis supervisors. 2022 EPFL/Alain Herzog - CC-BY-SA 4.0
Scientists from EPFL and the University of Lausanne have used a chip that was originally designed for environmental science to study the properties of biocement formation. This material has the potential to replace traditional cement binders in certain civil engineering applications.
The chip has the size of a credit card and its surface is engraved with a flow channel measuring one meter from end to end and as thick as a human hair. Researchers can inject a solution into one end of the channel and, with the help of time-lapse microscopy, observe the solution’s behavior over several hours. Medical scientists have used similar chips for healthcare applications, such as to examine how arteries get clogged or how a drug spreads into the bloodstream, while environmental engineers have applied them to the study of biofilms and contaminants in drinking water.

Now, a team of civil engineers at EPFL’s Laboratory of Soil Mechanics (LMS), together with scientists from the Faculty of Geosciences and Environment at the University of Lausanne (UNIL), have repurposed the chip to understand complex transport-reaction phenomena involved in the formation of new kinds of biocement. Ariadni Elmaloglou, a PhD student, together with Dimitrios Terzis, one of her thesis supervisors from EPFL’s Laboratory of Soil Mechanics (LMS), injected biocement solutions into microfluidic chips resembling different types of sand to see how the minerals form and the flow responds. Besides the sand types, the other main biocement ingredients – calcium and urea – remained the same. “Thanks to the chip, we were able to observe variations in biocement mass distribution in the different mixtures,” says Elmaloglou. “For instance, we could see where minerals were formed and which mixtures can lead to superior mechanical properties across the long flow path. Due to its miniaturized volumes, the chip enables us to perform multiple experiments with different mixtures in order to design efficient biocementation protocols.”
Due to its miniaturized volumes, the chip enables us to perform multiple experiments with different mixtures in order to design efficient biocementation protocols.
Meter-long testing
The engineers’ findings have just been published in Scientific Reports, a Nature portfolio journal. Theirs is the first study to examine biocement formation over the length of a meter in real-time, which is important for many potential applications such as crack repair, carbon storage and soil remediation (see box). All the data have been made available in open-source format in order to encourage further research on this topic.
Meanwhile, the LMS engineers have already started the next step of their study. “The chip makes it easy for us to test biocements made with aggregates of recycled materials – like glass, plastic or crushed concrete – rather than sand,” says Terzis. These biocements could help mitigate the construction industry’s carbon footprint, or even revolutionize the industry altogether. “The industry still relies heavily on concrete, even though the ingredients used to make it – especially sand – are getting harder to source. Our study shows that a cross-disciplinary approach can go a long way towards changing that. But we need to be open to methods from other research fields.”
For his PhD thesis at LMS, Dimitrios Terzis developed a new kind of biocement made with bacteria and urea. The process involves the use of calcium carbonate (CaCO3) crystals to bind soil particles together, instead of cement clinkers. The result is a material that’s bio-based, easy to use, resistant and fairly low cost compared with existing binders, including cement, lime and industrial resins. Resins in particular can become relatively unstable over the long term, can contaminate the soil with microplastics or toxic compounds, and can increase groundwater alkalinity to levels above acceptable limits.
The EPFL-developed biocement can be produced on site cheaply and at ambient temperature, with only a small amount of electricity required. Operators can adjust biocementation levels to their specific needs. If only a small amount of CaCO3 is added, operators obtain a sandstone-like result that’s resistant enough to withstand the earthquake-induced shear stresses that can lead to soil liquefaction. Other applications can help resolve slope stabilization problems or restore existing foundations. If more CaCO3 bio-minerals are added, the result is a mixture that can be used as a construction material or for waterproofing soil.
To take their technology to market, Terzis and Prof. Lyesse Laloui founded MeduSoil, an EPFL startup, in 2018. The firm has already carried out field demonstrations in Switzerland and abroad.