Balancing Cost and Precision: Optimal Ordering for Selective Assembly
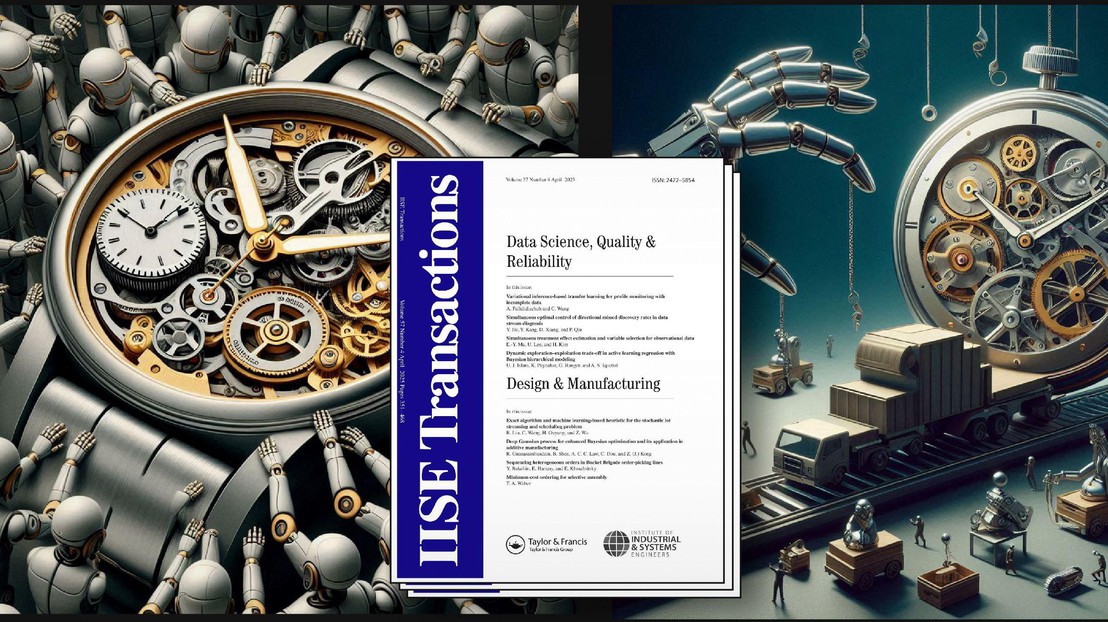
© 2025 EPFL
Prof. Weber’s latest research, “Minimum-Cost Ordering for Selective Assembly,” features in the current issue of IISE Transactions, the flagship journal of the Institute of Industrial and Systems Engineers for over 55 years. The study provides a cost-optimal approach to ordering components for high-precision assembly, helping manufacturers cut costs while meeting strict quality standards.
Selective assembly is critical in precision manufacturing, where parts are sorted into tolerance classes and matched to achieve tight specifications. However, ensuring precision often leads to costly material overage due to unmatched components. This research offers a new framework to minimize input costs while maintaining required performance, equipping manufacturers with practical tools to optimize procurement strategies.
Prof. Weber’s paper focuses on systems with two input types—such as hairsprings and balance wheels in watchmaking—and develops a closed-form approximation that simplifies the complex cost-precision tradeoff. A key insight is that not all inputs should be treated equally. The research shows that lower-cost components often serve as “buffers,” ordered in excess to maximize the use of high-value parts. For instance, watchmakers routinely over-order the cheaper hairsprings to avoid mismatches with expensive balance wheels. As precision demands increase, these overage costs can skyrocket, making smart ordering strategies essential.
Beyond watchmaking, the findings apply to industries like automotive and electronics, where selective assembly ensures product reliability. The study highlights how increasing the number of matching classes improves precision but also drives up material waste. The proposed framework helps manufacturers strike the right balance, reducing procurement costs without sacrificing quality.
Building on the author’s prior research [2, 3], the current publication [1] allows for selective-assembly systems with an arbitrary number of matching classes, retaining simplicity and interpretability. In addition to addressing the cost implications of assembly precision, the study highlights how the scalability of the framework renders it applicable to diverse manufacturing contexts. The watchmaking example illustrates how precision requirements drive costs, underscoring the need for a measured approach in a random-yield environment.
Overall, this article offers valuable strategies to manufacturers seeking to enhance output precision without compromising cost-efficiency—a practical guide for navigating the delicate balance between product quality and profitability. It is also featured in the current issue of the ISE Magazine, Vol. 57, No. 3 (March 2025), which is the member magazine of the Institute of Industrial and Systems Engineers.
This research is part of an ongoing project on precision manufacturing at the Chair of Operations, Economics and Strategy (OES) at EPFL, and the current results follow the investigation of matching of random parts with just two matching classes [2], and the robust design of matching classes in [3].
Abstract: We consider the minimization of input cost for a selective assembly system that features two random inputs and a finite number of matching classes. This setup frequently arises in high-precision manufacturing when input tolerances are not tight enough for the required output precision. We determine optimality conditions for the cost-optimal input portfolio given an expected-output target, first using a normal approximation of the multinomial binning distribution, and second employing a simple upper envelope of the output objective. We show that the relative error tends to zero as the production scale becomes sufficiently large. The envelope optimization problem also yields a closed-form solution for the cost-minimizing inputs as well as total costs, which are easy to understand for managers. A numerical study tests the practicality of the envelope approach. The latter can be used as seed for a numerical solution of the exact problem, as well as a closed-form approximation, which allows for an analysis of structural properties.
[1] Weber, T.A. (2024) “Minimum-Cost Ordering for Selective Assembly,” IISE Transactions, Vol. 57, No. 4, pp. 454—468.
[DOI: 10.1080/24725854.2024.2347918; open access]
[2] Weber, T.A. (2022) “Optimal Matching of Random Parts,” Journal of Mathematical Economics, Vol. 101, Art. 102688.
[DOI: 10.1016/j.jmateco.2022.102688; open access]
[3] Weber, T.A. (2021) “Minimum-Error Classes for Matching Parts,” Operations Research Letters, Vol. 49, No. 1, pp. 106—112.
[DOI: 10.1016/j.orl.2020.12.003; open access]