A step closer to reusable rockets
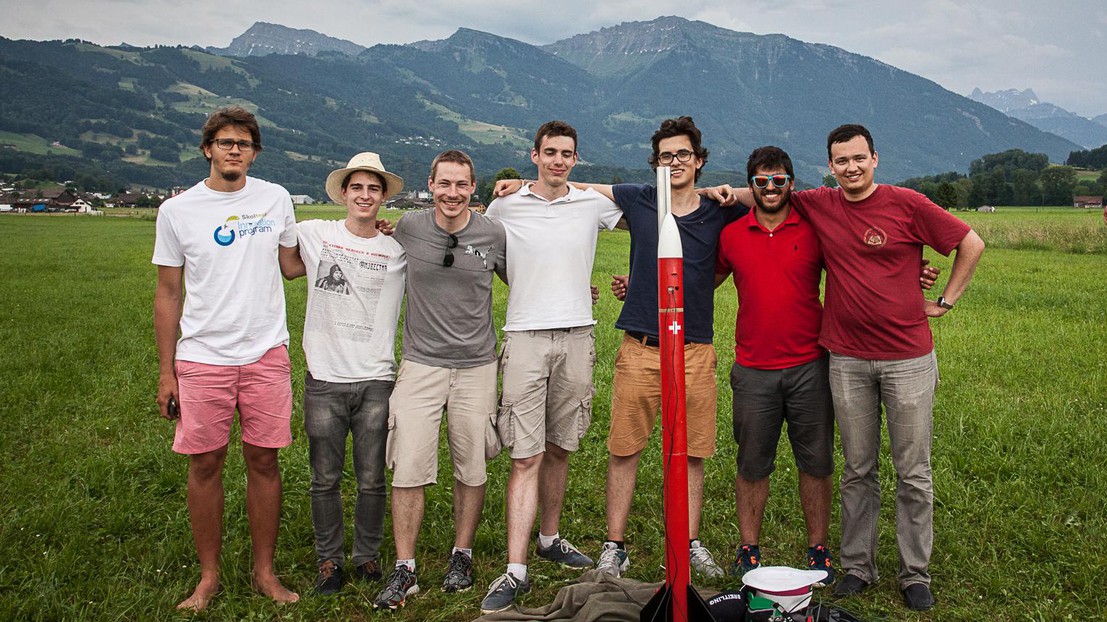
© R. Pictet
Summer Series on Student Projects: Danylo Malyuta and four other mechanical engineering students have developed an unusual miniature rocket equipped with an onboard system for modifying its attitude mid-flight. This represents a small step towards rockets that can land vertically.
“Interplanetary travel is our future, and it will require vessels that can be reused.” Danylo Malyuta has vision. With four colleagues who, like him, study mechanical engineering at EPFL and are passionate about space technology, Danylo designed and produced a miniature rocket with the support of the Space Engineering Center (eSpace). The device, around 1.5 meters long and sporting a powerful engine, is not your traditional model rocket. The real innovation is the control system, which the students invented for their Bachelor’s project. “Our goal is to develop rockets that can achieve a soft, vertical landing,” said Danylo.
A rocket capable of making a precision landing is still a way off. But over the course of five launches the team got past the first major hurdle, which was to stabilize the device vertically at low speeds, specifically when it reached the highest point in its flight, at an altitude of nearly 200 meters.
The control system developed by the students consists of a pressurized CO2 gas canister equipped with four valves that feed out the sides of the rocket fuselage. The system kicks in four seconds following launch, after the engine – designed by a US model rocket association – has already finished its burn. When the control system valves open, pressure is released from the pressurized CO2 reservoir. This creates jets whose thrust modifies the attitude of the rocket at the desired point in time.
For the system to function properly, special attention is paid to the structure of the rocket and the weight of the various components. Each of the five students contributed his own expertise. Danylo handled the electronics side of things, i.e. the onboard computer located in the nose. Raimondo Pictet ran the flight behavior simulations. Mikael Martins Gaspar developed the launch station and the ignition system. Gauthier Rouaze dealt with the design and production of the payload, including the valves, and helped Xavier Collaud in building the booster. Xavier was also in charge of the rocket design, including the fins.
An unusual device
“The shape and size of the fins are key,” said Xavier. They determine the location of the center of pressure relative to the center of gravity, which is a fundamental piece of information for ensuring optimal stability and thrust.”
“With 60 bars of pressure and 200 newtons of thrust, it’s a unique and highly sophisticated engine,” said Nikolay Mullin, the project supervisor at eSpace. “This experience allowed the students to acquire some basic techniques, which also apply to the construction of large-scale rockets.”
Danylo Malyuta hopes to continue this experience by developing new and better prototypes. “We’re looking mainly at testing a more powerful reaction control system and maybe even movable fins.”
Picture: ©A.Herzog, EPFL 2015. From left to right, Xavier Collaud, Nikolay Mullin and Danylo Malyuta.
For more information on the project, check out the eSpace website: http://espace.epfl.ch/flyARocket