A bench out of glass that's as resistant as steel
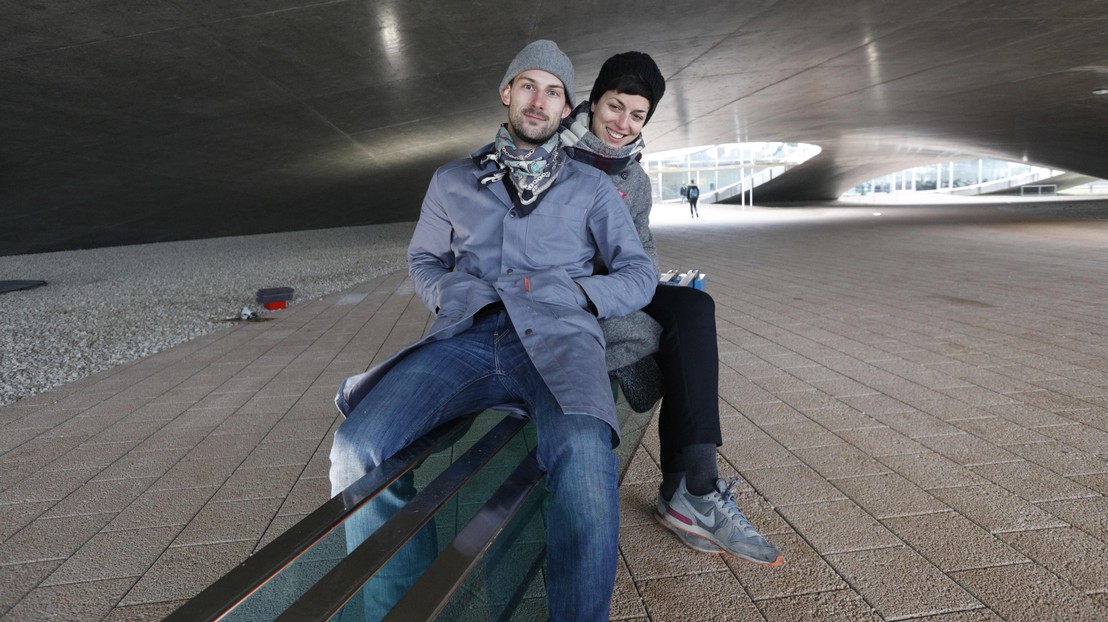
Alexander Wolhoff and Jagoda Cupać. © Marc Delachaux / EPFL 2017
A PhD student in civil engineering at EPFL and a recent architecture graduate joined forces to make a bench out of exceptionally resistant glass. Several companies broke new ground in support of this highly innovative project.
By combining her know-how with that of EPFL architect Alexander Wolhoff, Jagoda Cupać, doctor in civil engineering, has proven that glass can be transformed into an ultra-resistant material. Their project? Creating a six-meter-long glass bench named ATLAS. Several companies contributed to the project’s success using processes and materials that were new to them. The ATLAS bench is a true technology prototype and will be on display for a semester at the Rolex Learning Center.
In contemporary architecture, glass has long been used for so much more than just windows. It's everywhere – in roofs, stairs, walls, floors and beams – and that's not likely to change anytime soon. And so like Atlas, the mythical figure condemned to hold the sky aloft for eternity, the engineers had an epic challenge of their own, that of turning glass into a load-bearing material that is as resilient as steel or concrete without losing its trademark transparency.
Reinforced and post-tensioned glass
Cupać first began working with glass for her Master's degree in civil engineering in Croatia. Then, for her thesis at the Resilient Steel Structures Laboratory (RESSLAB), she tested glass beams that had been reinforced and post-tensioned with pieces of stainless steel. The properties of these beams were unknown and had barely been studied before at EPFL. During the post-tensioning process, the steel is stretched mechanically before being attached to the glass beam to make it more resistant.
The researcher conducted dozens of bending resistance tests to identify the most resilient beam system. “The glass beams are post-tensioned using stainless steel bars that are attached at the beam ends and glued along the glass edges. Due to the applied prestress, the bending resistance of the beams is increased. In case of failure of a glass roof or floor due to exceptional load or vandalism, for instance, this system can ensure that everybody inside and outside the building is safe because the steel bars take over the tensile forces and make the glass more ductile – meaning that it can sustain significant deformations. This prevents the structure from collapsing immediately and without warning,” explains Cupać. The results of her research challenge preconceived ideas about the fragility of glass, which can in fact be made as resilient and ductile as more conventional load-bearing materials.
Three types of prestressed glass
Alongside the theoretical component of her thesis, Cupać suggests three types of post-tensioned glass beams that can be directly applied in construction. That's how she got the idea of joining forces with Alexander Wolhoff, who has just completed a Master's in architecture at EPFL. “Working with an architect meant that I could apply my thesis findings directly to the construction sector. Adding an artistic angle made the whole project more interesting,” says Cupać. Wolhoff also highlights the importance of sharing knowledge: “What made this combination of two different areas of expertise so enriching was that we had to pull each other out of our comfort zones and be inventive. The ATLAS project wouldn't have been possible without this in-depth exchange and our willingness to listen to each other.”
The ATLAS project
So that's how ATLAS came to be. It is a bench composed of three post-tensioned glass beams reinforced with steel, and two support blocks made out of high-performance fiber-reinforced concrete (HPFRC). These blocks are tinted with a shiny surface, and transfer the load from the beams to the ground. Wolhoff developed a special type of concrete for the project, based partly on his own research. EPFL's Structural Maintenance and Safety Laboratory (MCS) helped produce the two supports. Christophe Loraux, a PhD student in the MCS Laboratory, got involved in the project, advising Wolhoff to use HPFRC instead of conventional concrete, which has several drawbacks for this type of application: “It made sense to use HPFRC because it goes well with glass. It meant we combined two highly resistant materials that are stable over time.” Perhaps this is another nod to the Greek mythical figure.
The HPFRC made with synthetic fibers, which was developed by the MCS Laboratory, was thus chosen because it offered numerous advantages: it’s easy to cast, mechanically resistant – both when compressed and in terms of tensile strength – and doesn’t wear over time. The resulting material can cause confusion: it looks more like porcelain than conventional concrete. The ATLAS project plays with this visual aspect: the bench resembles something between glass and porcelain, and onlookers would be forgiven for thinking it is fragile.
Sparking the curiosity of sponsors
To get the other materials, the researchers had to convince potential sponsors, as Cupać explains: “One Zurich-based company specialized in the field of post-tensioning, commonly applied in the construction of concrete bridges, had never heard of this glass-steel combination and agreed to provide us the steel. And the adhesive we chose tends to be used only in electronic components, even though we think it has great potential for other applications. It was all put together by a major constructor of glass facades that hadn’t heard of this type of beam before either.”
The ATLAS bench will be showcased for the first time outdoors on the EPFL campus before being moved to a more permanent, indoor location. Cupać and Wolhoff are still looking for the perfect spot.
Reference
The ATLAS project is the result of a collaboration between EPFL's RESSLAB, ALICE and MCS Laboratories and was supported by BBR Network Group, Huntsman, AGC VIM and Félix Constructions.